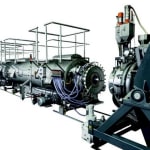
Complete extrusion lines for high performance, energy and material savings in pipe and profile extrusion
For large diameter PO pipe extrusion (up to 2.6 m), the new solEX NG single screw series offers outputs up to 2,500 kg/h. The newly designed, groundbreaking processing unit enables up to 10°C lower melt temperatures, an optimized, constant pressure build-up and therefore reduces maintenance costs and lowers energy costs by up to 15%. In production lines for both mono- and multi-layer PO pipes, battenfeld-cincinnati’s proven helix II VSI pipe heads ensure best distribution of the melt with their two-step distribution concept. The combination of solEX NG and helix II is especially well suited for large diameter PO pipe extrusion. For this application, battenfeld-cincinnati offers complete lines for diameters up to 2.6 m.The new conEX NG conical twin screw extruder is ideal for the production of PVC pipe and profile. It features a longer pre-heating zone and an optimized screw design for higher outputs (up to 250 kg/h for profile and up to 450 kg/h for pipe). The new geometry concept minimizes wear, and a great variety of material blends can be processed with just one screw configuration. The conEX NG is also an excellent choice for co-extrusion, e.g. in window profile production. Several space-saver and pedestal designs can be optimally adapted to the main extruder.
For large diameter PVC pipes that are used for water management, the parallel twinEX twin screw extruder range is also ideally suited. Their 34D processing unit serves to expand the processing window and improve the quality of the melt, while optimized screw concepts ensure high outputs of up to 2,500 kg/h for pipe and up to 600 kg/h for profile. Complete PVC pipe production lines include spider pipe tooling designed for processing a great variety of material blends. The special geometry ensures even and accurate wall thickness distribution and low pressure build-up.