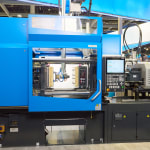
Sumitomo (SHI) Demag continues its strong commitment to sustainable development. Following its motto Act! Sustainably, this year, at the Plastpol fair on May 23-26, the company will present 2 energy-saving production cells based on on high-speed, fully electric injection molding machines, dedicated mainly to the technical and packaging industries.
High-speed full-electric IntElect S 75 ton with in-house robot SAM-C
Sumitomo (SHI) Demag will demonstrate the production of a 4 cm diameter cover for a motor component on a new high-speed electric injection molding machine IntElect S series with a clamping force 75 tons, integrated with a SAM-C handle & place robot. The detail will be produced in a four-cavity mold, in a cycle time 28 seconds. Then, the in-house designed robot SAM-C, the detail will be removed from the mold and placed on the conveyor belt. The most surprising thing about the entire process is the high energy efficiency of the production cell and the injection molding machine itself. The energy consumption of the machine is on average only 1.4 kWh. Such low energy consumption is possible thanks to the improved design of the injection molding machine, equipped with high-performance, low-inertia direct drives and high-performance ball screws. These components have been specifically designed to reduce energy consumption to just what’s needed to melt and transport the material, making the new version of the IntElect S series highly efficient and energy efficient. One of the key process advantages of electric drives is the ability to control the linear axis at speeds exceeding 500 mm/s. With energy prices rising rapidly, countering the impact of rising production costs through higher productivity, process repeatability and reduced waste is increasingly imperative from a competitive point of view. For these reasons the IntElect S version is so popular in the market.
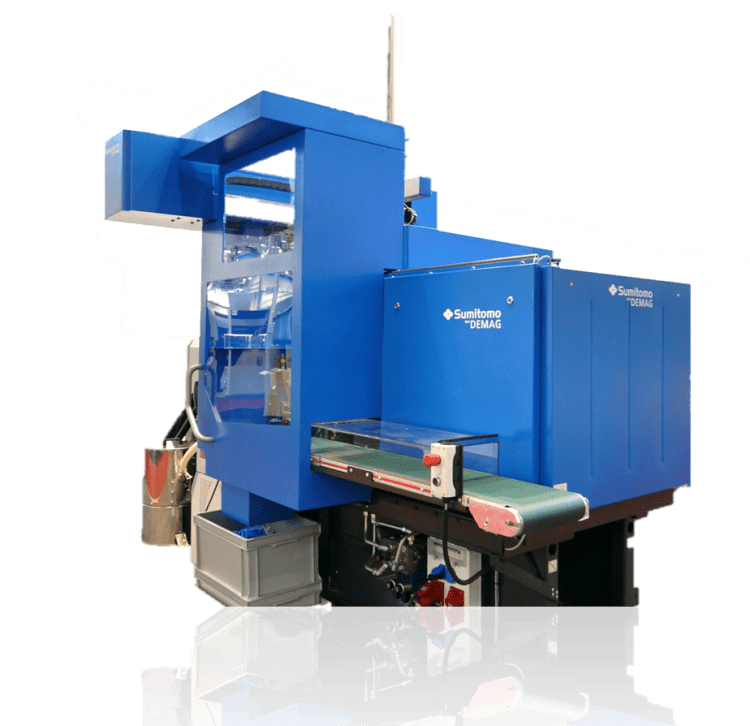
Along with the high-speed electric injection molding machine IntElect 75 ton, the company will also showcase its automation capabilities using its own brand SAM-C handle & place robot integrated on the machine. The robot line called SAM is designed to minimize maintenance by using proprietary servo motor technology and a low-maintenance guides. Specifically designed to optimise production on Sumitomo (SHI) Demag injection molding machines, the robots SAM-C can significantly reduce overall footprint of a self-contained cell while simultaneously improving user-friendliness of the machine controls. The undoubted advantage of the SAM-C robot integrated with the IntElect S 75 is the operation of both devices from the machine panel and the ability to save process data in one place in the machine's memory. The new IntElect S 75 ton version, combined with the compact SAM-C robot, integrated housing and conveyor belt, will perfectly illustrate the synergy between the machine and the robot, creating a fully equipped, compact production cell.
To demonstrate the energy and economic efficiency of the production cell, an exciting live comparison is going to be carried out at the booth, by testing the energy consumption of an electric kettle and an injection molding machine. A kettle will be placed next to the IntElect S 75 ton, and energy consumption will be measured for both. Thus visitors at the booth can see on their own which device is more economical.