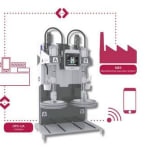
Mark Ostermann, Sales Manager at Elmet says: "With the new OPC-UA connection, processors have the possibility to store recipes and parameters together with the machine data, and they can enter parameters for the dosing system directly into the control unit of the injection molding machine and call them up from there. The data of the dosing system can be implemented easily into the production control system. No additional expensive license is needed because the injection molding machine is established anyway in the control system. Elmet is thus making a valuable contribution to improving user friendliness even further and to minimizing the risk of error in the day-to-day business."
The TOP 5000 P is designed for large-series production of high-quality parts. It is suitable for shot weights in a range of less than 0.1 g to several kg, and can manage containers with a capacity of between 20 and 200 liters and material viscosities from 9,000 mPas to 3 million mPas, even with large viscosity differences between the components. Only recently, the SHORE-MIX extension stage came onto the market, in which three dosing systems comprising two A and two B components produce a mix with exactly reproducible Shore hardness.
Ostermann continues: "Our TOP 5000 P is equipped with two separately functioning control circuits, one of which ensures over 99 % emptying of the containers, while the other makes sure that the volumes fed into the process correspond exactly to the target figure. Consequently, this system is especially valuable when the process window is tight and the start-up conditions are difficult. And, with an additional additives control solution, we achieve constant, highly accurate dosage, irrespective of sediments, wear and tear and viscosity differences."
Source: Elmet