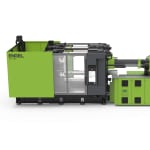
As the demands on productivity and energy efficiency continue to rise, integrated system solutions to support cost-effective injection moulding are rapidly gaining in importance. At Chinaplas 2023, which takes place from 17 to 20 April in the Chinese city of Shenzhen, Engel, the injection moulding machine manufacturer and system solution provider, will set up challenging applications to demonstrate how combining the ideal machine with smart digitalisation can maximise overall efficiency. Also at the Chinaplas event, the new iQ hold control assistance system will be making its Asian première.
“All of us are very much looking forward finally to re-establishing personal contact with our customers, partners and the sector as a whole in Asia,” says Gero Willmeroth, President Asia and Oceania at Engel in the run-up to Chinaplas. The event opens its doors in Shenzhen on 17 April following the Covid-enforced break. “Now that travel restrictions have eased, we are expecting more visitors from across Asia to attend the trade show. We are now in the post-Covid era and perceive a spirit of optimism that will also blow through Chinaplas.” Engel will welcome visits to its stand of the usual dimensions in hall 11, with four machine exhibits alongside Expert Corners devoted to trending themes.
Coining with high precision moulding
The production of mirrors for head-up displays of polycarbonate using a servohydraulic duo 2460/500 injection moulding machine calls for the highest precision moulding. Projecting a sharp display image on the vehicle windscreen depends on a perfect injection moulding outcome. The coinmelt coining process and the ingenious design of the dual-platen clamping unit both contribute to this. Platen parallelism is controlled by four individual pressure pads as the clamping force builds up. This ensures the precise parallelism of the mould halves throughout the injection moulding process when using coining. In this way, the coining process can produce asymmetrical components with maximum precision moulding. With low holding pressure, the melt is evenly distributed over the projected component surface. The material is protected, which is why coining is mainly used for optical parts made of transparent plastics. The convex head-up mirrors underline the high potential in this area. Here, the injection point is away from the centre of the component.
Engel will be presenting an automated production cell. An Engel viper robot will remove the parts from the mould and place them on the conveyor belt. Where Engel supplies the injection moulding machine and robot as part of an integrated system solution, these access a shared database and coordinate their movement sequences precisely. This results in a shorter cycle time in many cases because the robot can start moving in during the mould opening movement.
For this exhibit, Engel teamed up with a local mould producing partner: Skymold, based in Ningbo City, China. Working with local partners ensures a high degree of cost efficiency even in the case of sophisticated and innovative technologies while shortening delivery times for the system as a whole. The Engel duo machines are also produced locally for the Asian markets. The large-scale machine plant is located in Shanghai.
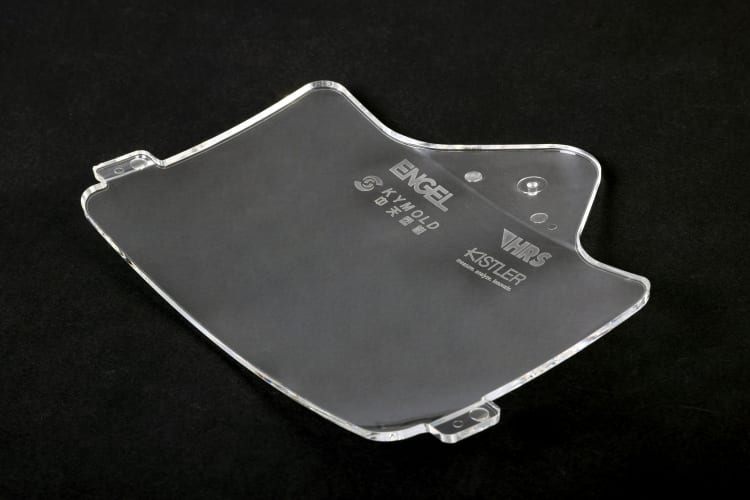
At Chinaplas 2023, ENGEL will use a servohydraulic duo 2460/500 injection moulding machine to produce mirrors for head-up displays in a high-precision coining process.