e-mac improves productivity per unit of area in the cleanroom
In the medical sector, Engel is showcasing a high-precision and, above all, space-saving all-electric application: needle protection caps are being produced on an e-mac 265/130 - equipped with the Engel cleanroom package - in a premiere at Fakuma. This means that the compact e-mac series is now also available for space-saving production of medical parts in cleanroom applications. The 96-cavity mould comes from Kebo AG and was developed specifically for secondary packaging. Secondary packaging does not directly touch the active ingredient and is mainly used to protect and identify the medical device. Moulds with a large number of cavities, like the mould by Kebo, require high precision and dynamics in the injection process – and this is exactly what the new injection unit 265 ensures. The cycle time is a fast 6.2 seconds.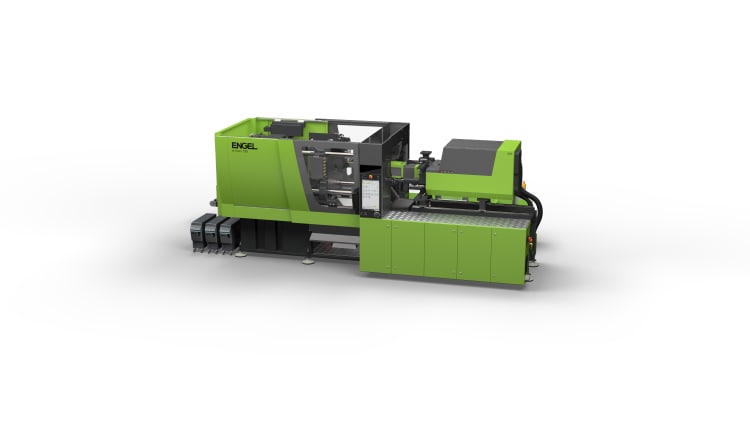
ENGEL produces needle protection caps for the medical sector on an emac 265/130.
On show for the first time, box transfer system reduces manual intervention
The box transfer system is a further innovation that supports optimum use of the production cell in partially to fully automated production. The injection-moulded needle protection caps drop out of the Kebo mould into a delivery chute and are transported from there by a Z conveyor belt to a box waiting on another conveyor belt. This box has a capacity of 30,000 units. Once full capacity is reached, the box is cycled forward on the conveyor belt. All told, there is space for four boxes of this type on the belt. The box transfer system can be connected to an automated guided vehicle (AGV) system - independently of the manufacturer. Besides the digital interface, all that is needed is preparations in logistics to allow the AGV to dock with the box transfer system and accept the boxes.

The box transfer system offers optimum connectivity to partially and fully automated production.
Combinations for optimum temperature control
Both the duo 500 and the e-mac 130 show how smart temperature control works. The two production cells combine e-flomo plus with eco-flomo plus to manage the various aspects of temperature control in the best possible way: while e-flomo plus takes care of mould temperature control, eco-flomo plus is used for hot runner cooling, and more specifically for flow rate monitoring. All manifolds are clearly displayed by the iQ flow control smart assistant.
Solutions deliberately reduced to the essential that enable high-performance, efficient injection moulding production - these are the requirements that Engel is squaring up to for its customers at Fakuma 2023.
Engel at Fakuma 2023: hall A5, stand 5204