Smart assistance boosts process consistency
Injection moulding machines in the e-mac series promise ample flexibility when it comes to the integration of smart assistance systems. Alongside precise electrical axes, iQ systems from Engel enhance process stability and product quality by ensuring ideal process settings from one cycle to the next.
For example, iQ weight control analyses the pressure profile during the injection process and compares measured values by means of a reference cycle. The injection profile, switchover point and the holding pressure profile are adjusted to the current conditions for every cycle, which keeps the injected volume constant during the entire production run. In this way, consistently high product quality is achieved. Rejects are proactively prevented, saving raw materials and energy.
Potential is particularly strong in the processing of recycled materials, which are naturally subject to greater batch fluctuations than new materials. Smart assistance systems are thereby actively supporting the circular economy. Processed plastic waste can also be used in higher-value applications with the help of smart assistance.
For precision applications with cycle times of over four seconds, the e-mac is the solution with the greatest overall efficiency for many applications in the field of all-electric injection moulding machines. Beyond the packaging industry, the e-mac is used in the technical moulding, teletronics and medical technology sectors, among others.
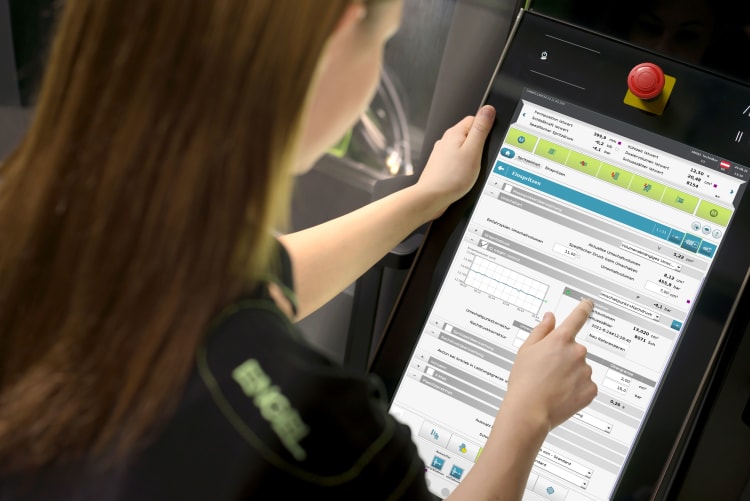
iQ weight control compensates for process fluctuations before rejects are produced. The huge potential of digitalisation in terms of greater efficiency and higher quality will be demonstrated at the Engel stand.
Local partners cutting time to market
Founded in 1945, Engel has steadily developed over the course of its history from a manufacturer of injection moulding machines to a system expert. As a single source supplier, the family-owned company provides turnkey production cells for sophisticated applications that not only include the injection moulding machines, but also the automation, process technology and Industry 4.0 technologies. Alongside injection moulding machines, the company’s development and production divisions create various types of robot, process technologies and digital solutions. Engel integrates other systems in collaboration with contracting partners and has built up a global network of partners to this end.
At Plast India, Engel will cooperate with Piovan on the peripheral systems. Just like Engel, Piovan maintains a strong local presence in India. The 32-cavity mould for the manufacture of flip-top caps and closures will be from Vasantha, a company based in Hyderabad. Engel clients around the world benefit from these close working relationships with local partners. Regional networks ensure short communication paths, fast times to market and more attractive prices for integrated system solutions.
Engel at Plast India 2023: Hall 7, stand FP-F-01