Engel adding recycled material to high-end visible parts
All-electric drive technology is the mainstay of the second machine showcased by Engel at Plastpol 2023. TV boxes with a high-gloss finish are being produced on an e-mac 465/160 injection moulding machine. What is special about this is that the boxes are made from 100 percent rABS sourced from post-consumer waste collection. The cavity is laser engraved to create an innovative rainbow pattern on the top side of the boxes, and there are fixtures for installing fans and connectors on the side surfaces. The ultra-thin design - the wall thickness is 1.2 mm - saves material. Conventional injection moulding would require a greater wall thickness.
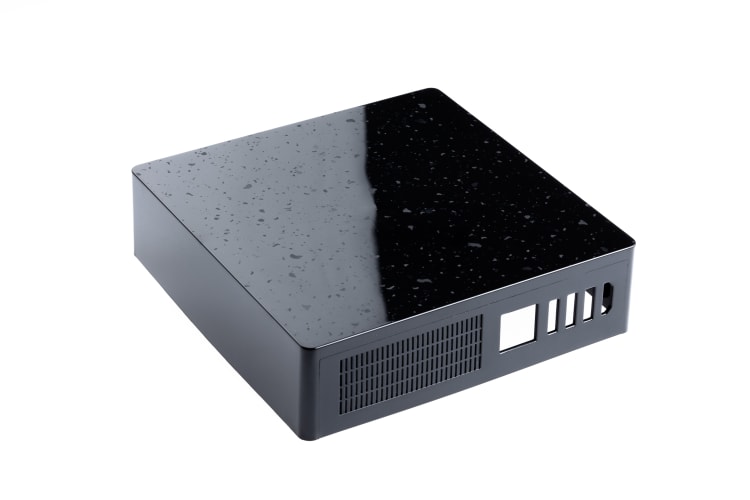
To achieve a closed material cycle for high-end visible components made of ABS, Engel is cooperating with technology expert Roctool (Le Bourget du Lac, France). The key to the premium surface quality of the recycled component is, on the one hand, mould temperature control based on induction technology. New energy-efficient, compact and air-cooled Roctool generators are used here.
On the other hand, smart assistance systems by Engel make a contribution to high quality in the processing of recycled materials. Since recycled materials are generally subject to greater batch fluctuations than virgin material, iQ weight control has a particularly positive impact in terms of achieving consistently high product quality in this application. At the same time, iQ melt control improves the homogeneity of the molten plastics by automatically adjusting the plasticising time to the optimum value for the application.
The application presented at Plastpol demonstrates the huge potential for the circular economy for manufacturers of household appliances, white goods, consumer electronics and telecommunications products. The proportion of virgin material can be significantly reduced, to zero in the best case. Already today, many manufacturers are taking back end-of-life equipment for recycling and returning it to production. Thanks to this combination of Roctool induction technology and smart digital assistance systems by Engel, even demanding housing parts with a very thin and complex geometry can now be produced from post-consumer recycled material in a cost effective and sustainable way.
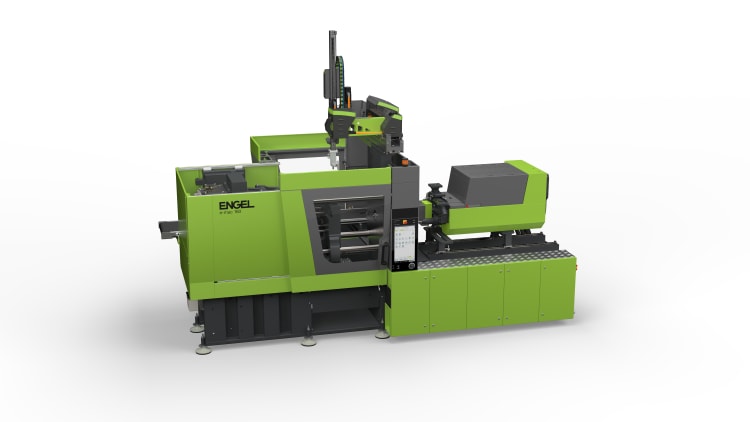
Pushing the circular economy forward together
Other system partners involved in the project's success include Moldetipo (Marinha Grande, Portugal), who built the mould, and Lavergne (Montréal, Canada), who provide the recycled material, INCOE (Rödermark, Germany) for the hot runners and Standex Engraving Mold-Tech (Treviso, Italy) for mould engraving.
Close collaboration along the value chain is essential for establishing a circular economy. This is why Engel is strongly committed to networking these companies on multilateral, horizontal platforms. They include the R-Cycle Initiative whose objective it is to introduce digital passports for plastics products. All information relevant to recycling is automatically recorded as early as the product manufacturing stage so that, for example, waste sorting plants can identify recyclable plastics more accurately and deliver single grade fractions for recycling. This approach puts an end to the downcycling that has been prevalent up to now by reusing the recycled plastics on a par or even with added value.
Engel at Plastpol 2023: hall F, stand 4