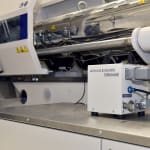
At the K 2019 in Düsseldorf, Wittmann Battenfeld will exhibit its products and applications under the motto “Enjoy Innovation” for the first time in hall 15 at booth C06. Wittmann Battenfeld has thus an additional 120 m² of exhibition space at its disposal, and from 16 to 23 October the company will now be presenting its innovative injection molding technologies, processes and applications right next to its key competitors.
Innovation has always been a top priority at Wittmann Battenfeld. The company’s product developments are designed to offer customers maximum benefit and simultaneously to protect the environment and preserve it for future generations in a sustainable way. Apart from further development and optimization of machinery and equipment, which are setting benchmarks in the market in terms of energy efficiency, this is achieved primarily through the development and continuous improvement of the adaptive HiQ application and process technologies and use of ultra-modern software systems and technologies to enable the integration of machines, robots, auxiliary appliances and MES systems via Wittmann 4.0, plus sensor systems for machine condition monitoring, abbreviated CMS. Furthermore, the company is working together with partners on processing materials which at the end of their product life are 100% recyclable and/or completely degradable.
Key topic: intelligent machines with adaptive algorithms
The main theme of Wittmann Battenfeld's presentation at the K 2019 is to showcase intelligent machines with adaptive algorithms, which adjust themselves to the ambient conditions.
This will be demonstrated with an all-electric EcoPower 55/350 equipped with the software packages HiQ-Flow, HiQ-Melt and HiQ-Metering. A W918 robot from Wittmann and all auxiliary appliances connected with the machine, as well as the TEMI+ MES system, are integrated in the machine’s UNILOG B8 control system via Wittmann 4.0. The electronic mold data sheet will also be used on Unilog B8. The production cell linked together via the Wittmann 4.0 router is thus able to check whether the connected auxiliaries are sufficient for the selected product data set, or if additional equipment is needed.
At the Wittmann Battenfeld booth, this production cell will be used to present the HiQ functions in the form of specialist lectures and live demonstrations. On the EcoPower 55/350, polycarbonate clothes pegs will be manufactured with a 4-cavity mold supplied by Lechner, Austria. Using this fully integrated production cell, the advantages of integration via Wittmann 4.0 and the TEMI+ MES system can be clearly seen. In a live demonstration, the product HiQ-Flow will automatically compensate the effect of material viscosity fluctuations, thus ensuring stable parts quality and eliminating scrap. To avoid plastic waste, pieces of sprue and bad parts deliberately produced for demonstration purposes will be re-granulated in the new G-Max 9 granulator from Wittmann, and then directly returned to the machine hopper via the vacuum conveying device connected with the granulator.
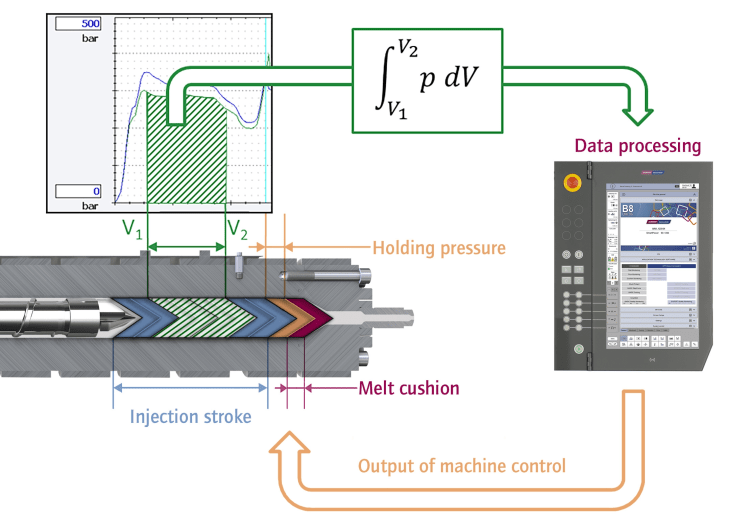
Schematic diagram of material viscosity-driven injection control
Launching of new VPower Combimould model with special automation package
At the K 2019, Wittmann Battenfeld will show its latest further development of the vertical machine in PowerSeries design in the multi-component version. On a VPower 120/130H/210V, a plug made of PA and TPE for the automotive industry will be manufactured with a 2+2-cavity mold. The complete automation system for the machine is designed by Wittmann Battenfeld Deutschland in Nuremberg. In this application, a Scara robot and a WX142 linear robot from Wittmann are used, which insert the wrap pins, transfer the preforms, then remove and deposit the finished parts.
Introduction of new EcoPower Xpress in medical version
Another new product at this year’s K will be a high-speed EcoPower Xpress 160/1100+ in a medical version. On this machine with 1,600 kN clamping force, PET blood tubes will be produced with a 48-cavity mold supplied by Pass Card, Taiwan. To meet the stringent requirements for PET plasticizing, this machine has been equipped with a modified high-performance screw. In addition, a special drying hopper has been mounted above the injection unit, where the granulate is dried by a frequency-controlled Drymax 300 dryer from Wittmann. The tubes will be removed from the mold and deposited in transport boxes by the new Wittmann high-speed robot. The robot controls a box exchange device, which removes every full box and replaces it immediately with one of the empty boxes held ready, to ensure uninterrupted production of the tubes.
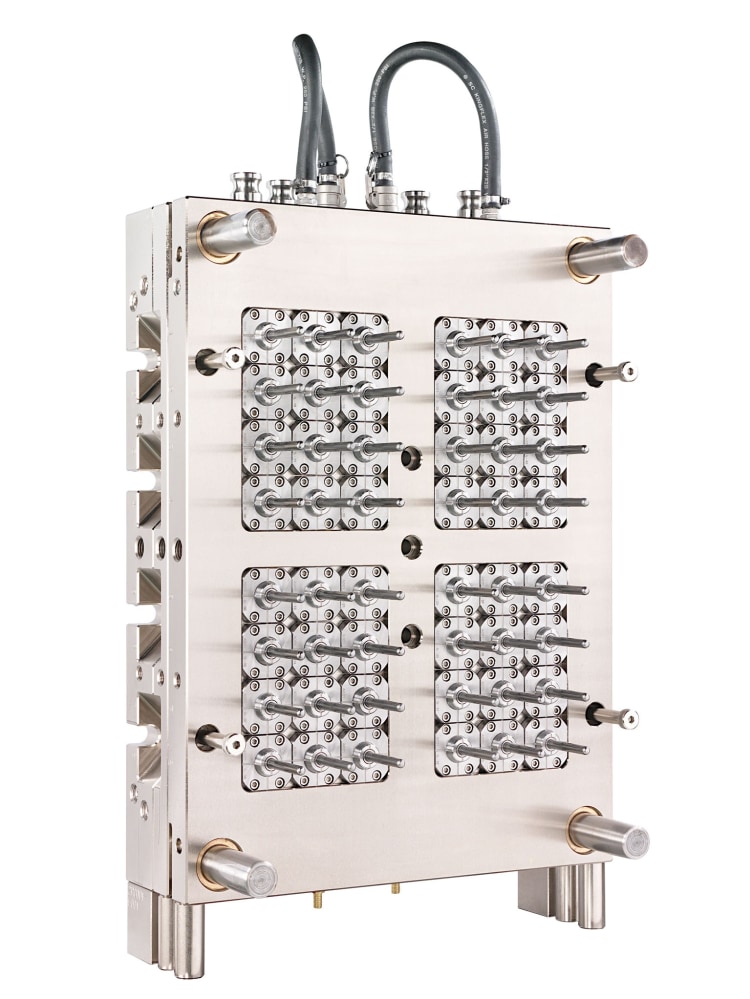
Mold for blood tubes