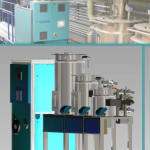
Whether for injection moulding of preforms or for extrusion into films, PET always needs to be dried and for amorphous basic materials it also needs to be crystallised. If recycled PET is processed in the form of postconsumer flakes for economic and environmental considerations, it is also necessary to remove quality-reducing, volatile impurities and by-products safely from the drying and moulding process.
The systems engineering necessary for these process steps, which has proven itself many times for PET treatment in the meantime, is in principle also suited for the treatment of biopolymers such as PLA (polylactide) and is currently being tested in operation in pilot projects.
A Somos D 200 dry air dryer (air flow rate 200 m3/h), which is exemplary for the new generation of stationary material drying systems was presented few weeks ago. It can be modularly combined and flexibly expanded to a drying facility customised to meet the respective processing function with drying hoppers from 50 to 300 litres in volume. For PET processing in packaging applications, where material throughputs ranging from 500 to 2,000 kg/h are standard nowadays, correspondingly larger sized dryers and dryer hoppers are available.
A new, powerful controller (MH 25) now controls the triggering of the dew point-constant dry air with the D-dryer. In combination with additional design innovations it leads to a significantly more flexible application of the dryers. The Somos D 200 dryer can be, for example, “expanded” from nominally 200 m3/h up to 500 m3/h by adjustment in control technology. With this, the reliably dried material throughput can be increased from originally max. 100 kg/h up to 250 kg/h without extra hardware. This optional extension of the operating mode is even implemented in the design of the higher nominal sizes of the new Somos D-Dryer generation. At the same time, the also newly designed process control of the dryer’s rotary desiccant container leads to a significantly reduced time for the regeneration of the drying agent, so that the energy required for this can be used more effectively.
The another novelty launched by Mann + Hummel is new modular condensate separator. With this, the return air from the drying hopper which is essential e.g. for the processing of PET flakes can be freed from all volatile matters (for example, monomers, by-products and dust particles). Controlled separation and collection of these material impurities makes it possible to transport them directly to waste recycling.
The modular condensate separator consists of three serially connected units: the pre-filter module for dust separation from process air, the cooling unit for cooling contaminating substances below the dew point, and finally a demister module as the actual condensate separator. All modular units are easily accessible and can be cleaned quickly and easily. The modular design facilitates flexible adaptation of the modular condensate separator to changing manufacturing conditions through expansion and combination of the individual units.