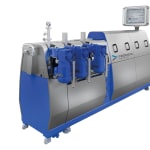
For the fifth time, Feddem GmbH & Co. KG, will be exhibiting at the K trade fair in Hall 15, Stand A42. In addition to the diverse extruder models of the manufacturer of extrusion and compounding systems, the focus of the trade fair presence will be on some new developments in peripheral technology and augmented reality applications.
On its booth, Feddem will present the current model of the twin-screw extruder FED 26 MTS with auxiliaries for small-volume production in laboratory or pilot plant applications. The exhibit is equipped with the following accessories:
- The basic extruder with 32 L/D and a 10 L/D extension module, 34 kW installed drive power and max. screw speed of 1200 rpm.
- An FSB side feeder in standard version
- An FSV vacuum side degassing system
- The FSK strand head with Feddem's patented curved die plate.
- The new FSB-V side feeder with vacuum support
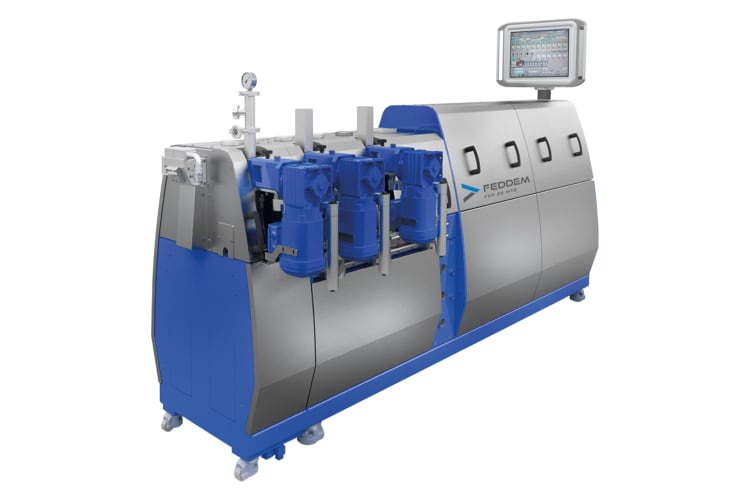
Twin-screw extruder Type FED 26 MTS with extension module and auxiliaries
"The new Feddem FSB-V side feeder with vacuum assistance has been developed to optimise side streams into the compounding process," says Klaus Hojer, Business Development Manager at Feddem. "Here, air is sucked out of the metered side stream before it enters the extruder. This enables a considerable increase in throughput rate of the overall process when adding lighter bulk materials to the process."
The machine builder is also presenting the second generation of its FRE cleaning unit for twin-screw housings. It has been fundamentally revised with a view to saving weight. The power supply is now provided by a rechargeable battery - the cable connection to a power outlet is no longer necessary. Due to the redesign for weight reduction, the weight of the entire device could be reduced to less than 10 kg, e.g., for a cleaning unit for a 72 mm twin screw extruder with 32 L/D process length. The functional principle of the device is also torque-compensated for the operator, i.e., any torque jerk from a blocking brush is transmitted to the extruder housing via the brush assembly’s distribution gearbox and does not reach the operator. This reliably protects the operator from jerky reaction forces and completely eliminates the risk of injury from torque jerks during operation. Older FRE cleaning units can be converted to battery operation, however, a factory adaptation of the drive shaft is required.
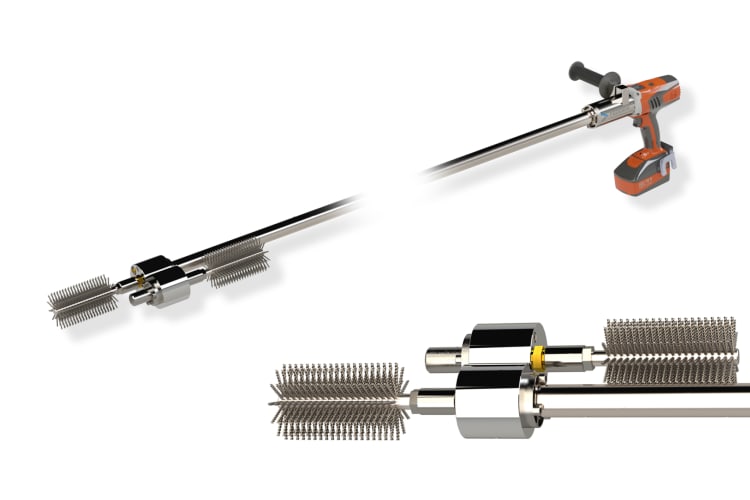
Feddem is presenting the second generation of the FRE cleaning unit for twin-screw housings to the trade public for the first time at K 2022.
Another highlight at the booth will be the demonstration of remote assistance using augmented reality and the extended digital provision of information.
"Here, we will have live demonstrations of the adaptation of the Oculavis share system to our products," explains Klaus Hojer. "In addition to real-time support of service work via the remote maintenance system (Remote Guidance), the system is also suitable for "step-by-step" guidance (Self Guidance) via the combination of live video information and case-specific information e.g. out of the trouble-shooting section of an operator manual - without being in direct contact with one of our experts."
The Sinzig-based company has taken a fresh look at the details of the plant components in the technology of the LFT pultrusion lines for the production of LFT-G long pellets in order to improve performance, quality and handling. The results are unprecedented tight tolerances in the fibre content in the pellets as well as the high repeatability of the achievable material properties of the LFT compound on different lines and line s with haul-off speeds of up to 60 m/min.
The use of a patented, modular impregnation tool plays a decisive role here. "Our extruder for preparing the melt is positioned parallel to the roving strands, which allows considerable savings in the space required for the line. The Feddem pultrusion plant requires only a little more installation space than a conventional compounding line. All maintenance access points for the individual plant components were designed in such a way that direct and fast access is possible in order to ensure the highest possible plant availability," explains Klaus Hojer.