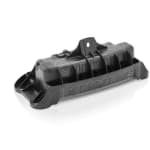
Minimum fiber content fluctuations
The precise metering of the PP long glass fiber content is mainly the result of the initial use of special gravimetric metering modules, which had previously only been used in the field of extrusion. A highly-concentrated PP-long fiber granulate with a 60 percent fiber content and equal parts polymer dilution (from PP) are metered and processed into plasticizing screws using two dosing units. Metering high concentrates requires a special development concept due to the complex flow properties. By using the C-Flex M Walkwand feeder from Motan-Colortronic, ensuring uniform mass flow for this granulate type is possible for the first time. "Fluctuations when setting the fiber content can be significantly reduced compared to conventional mixing concepts. According to current measurements, they are in an order of magnitude that corresponds to the batch fluctuations of the material manufacturer," says Jochen Mitzler, Head of Strategic Product Management for KraussMaffei.Processors are now able to adjust the procedure with more precision than ever before. These advantages especially come into effect during the manufacturing of safety-related components where particularly uniform and reproducible processes are required. A CX 300 – 1400 will produce a safety component just like this at Fakuma, namely an airbag housing for the automotive supplier Takata AG. Cycle times are under 40 seconds. Additional partners for the exhibit are Christian Karl Siebenwurst, Borealis Polyolefine and ONI.
The processing of highly concentrated long-fibers also offers real economic benefits. Compared to standard granulate, the material costs can be reduced. Moreover, the wall thickness is reduced due to the high strength of the long fiber granulate. "In conjunction with the great potential for lightweight construction that the FiberForm technology offers, the investment pays off very quickly and can therefore be considered a cost-effective lightweight construction solution," says Udo Gaumann, Manager Core Engineering Materials at Takata.
Space-saving multiple kinematics
The Fakuma trade show exhibit was equipped with two LRX linear robots in the TwinZ design. Both robots are mechanically coupled on the same Z-axis. Together, they assume the tasks of heating up semi-finished fiber components (composite sheets) and demolding the finished components. The multiple kinematics as well as the composite sheet feed unit are integrated into the standard CX 300 housing. This reduces the size of the installation area by up to 40 percent. Like the CX 300, both robots can be operated with the new MC6 Multitouch control system and provide increased operating convenience.An additional scale supports quality control. The components are weighed before they are placed on the conveyor belt. The weight information is returned to the MC6 control system online for documentation. The machine decides whether it is a good or reject part based on the defined tolerances. This ensures that stable production process controls are documented.