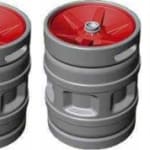
Brewers usually sell their beer in 20 liters, 30 liters or 50 liters stainless steel returnable kegs.
They face growing economic problems, linked to increasing stainless steel prices and transportation cost that results in a restricted cash flow. This is without taking into account environmental issues.
Lets take the cycle of a stainless keg sold to a US customer: cleaned with chemicals at the brewery, sterilized with steam, it is then filled and sent by boat. It arrives in a warehouse on the East coast and travels by truck to San Francisco (3000 miles away) to reach the clients premises. The empty keg then travels back to the warehouse, loaded again on a boat to Belgium and on a truck to the brewery. It is checked and sometimes repaired before it is cleaned, sterilized and filled again. The whole process can take up to 9 months.
- After careful study, multiple mechanical and quality tests and the modification of the keg filling line, 100 One Way Kegs were filled with our top quality blond beer Abbaye de Saint-Martin. The kegs were then put in the warm room for fermentation and will be sent to the United States of America within the next few days – he says.