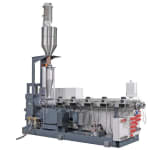
Hyundai Pipe is among the five largest manufacturers of pipes in South Korea and currently produces them in dimensions ranging from 100 to 1,500 mm for transporting fresh and waste water and for applications in the petrochemical industry. The company, which is certified according to DIN ISO 9001 and 14001, supplies both large companies such as ExxonMobil and Shell as well as small companies and is proud of its ability to provide the right pipe for any requirement. It already has three lines from the equipment manufacturer battenfeld-cincinnati in its production plant, which is equipped with eight extrusion lines in total and has a production capacity of 22,000 t/p.a.
Mr. Cho Sun Jae, President of Hyundai Pipe explains: "We decided to work with battenfeld-cincinnati again, based on the good relationship we have, our good working experience with the three lines already in our production and because battenfeld-cincinnati has a great deal of know-how in large diameter pipe extrusion. We have to replace old steel pipes with plastic pipes. The quality of HDPE pipes has already been proven, but there are still some parts of the market that do not see the advantages. Therefore, it is our responsibility to produce a good product and help it gain acceptance in the market. Hyundai Pipe aims to become a pioneer and market leader in plastic pipes."
To be able to manufacture pipes with huge diameters, the extrusion line needs an extruder with a suitably high plasticizing capacity. In the line ordered by Hyundai, this is guaranteed by means of a solEX 120-40 extruder, which achieves an output level of 2,200 kg/h with its processing length of 40 D. solEX extruders stand for top-quality performance, with excellent melt homogeneity, low melt temperatures, and low space requirements. Alongside the extruder, the tooling is the second key component of this line. This has the task of ensuring minimum ovality and minimum sagging, particularly for thick walls of more than 100 mm. The helix VSI-T+ system ensures low pressure build-up and operation independent of viscosity with its tried-and-tested combination of a spiral mandrel for initial melt distribution and a compact lattice basket for fine dispersion. The effective EAC (efficient air cooling) internal pipe cooling system guarantees high line speeds and excellent pipe quality. It also results in a shortened cooling section and thus a shorter total line length, which was also very important for Hyundai Pipe.