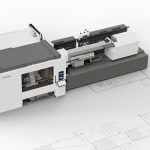
Starting with MetaPure recycling systems, equipment for preform production (including the Krones Prefero injection-moulding system added through the recent acquisition) and MHT tools and moving on to ErgoBloc for stretch blow-moulding, filling and labelling PET bottles, the company comes full circle with its machines and systems for the dry end. All of that is complemented by comprehensive digitalisation solutions and soundly based expertise in preform and bottle design, making the Krones Group the only supplier that can cover the beverage industry’s entire PET value chain with its own portfolio. But what exactly is the Prefero injection-moulding system, and what are the advantages it offers for the production of PET preforms and closures?
The injection-moulding machine in the Prefero system is a side-entry unit with fully electric clamping force and five-point twin toggle. Characterised by smooth running, low wear and a small footprint, the Prefero preform machine achieves hourly outputs of between 300 and 1,600 kilograms of PET. Its servo-electric drive uses high-dynamic-response synchronous motors promising second-to-none dynamics and energy-efficiency. Prefero can be relied on to provide homogeneous melt qualities and better colour blending and to process one hundred per cent rPET.
Sustainable solutions using only small amounts of packaging material for optimum product characteristics
More mould cavities per surface area and an adaptive injection-moulding process that permits ultra-fast cycle times combine to achieve higher performance levels with the same machine . A total of 144 cavities on a 400-tons machine make the PETX screw, which has been newly developed for the injection unit, the ideal option for the ongoing trend towards ever smaller and ever lighter preforms. Depending on the wall thickness and weight of the preforms, typical cycle times lie between five and 14 seconds. An intelligent hydraulic unit with adaptive drive prevents the oil from deteriorating so much at low temperatures. Moreover, it is now also possible to set lower temperatures at the dryer because the shearing and heating stages have been optimised.
Dryer, cooler and other peripherals have been integrated with Euromap 82. The post-cooling options include preform inside cooling. The high-dynamic-response removal drive is standard-fitted with a double belt and features up to four post-cooling stations in the removal plate. No fixed place at the movable side has been specified for the removal system, so it can be freely positioned. The PET production tools from MHT that are used by Prefero are known for being one hundred per cent industry-standard compatible. The standard coating for the cores is titanium nitride (TiN) and that for the neck rings is diamond-like carbon (DLC).
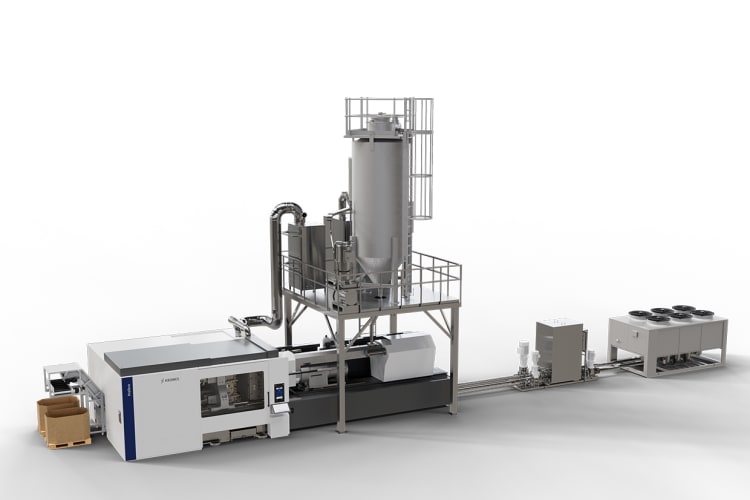
But what is really special is Krones’ philosophy of offering integrated systems, which by adding Prefero now also incorporate injection moulding. “The Prefero injection moulding system completes Krones’ line concept, in which several perfectly harmonised individual machines are combined to create a holistically conceived system. The points that really matter for Krones - and for Krones’ customers as well - are line efficiency and (technical) performance indicators. And that’s where we achieve the best possible results with a set-up consisting exclusively of Krones kit,” explains Jochen Hirdinia, Head of Plastics Technology.
“The Prefero injection moulding system completes Krones’ line concept, in which several perfectly harmonised individual machines are combined to create a holistically conceived system.” - Jochen Hirdina, Head of Plastics Technology at Krones
In line with the concept of continuously operating production, the direct link to the Contiform stretch blow-moulder creates yet more synergies by reducing the internal logistics involved. That is because after they have been injection-moulded, the preforms are passed straight to the blow-moulder, without any detours or interim storage. And that pinpoints further advantages of in-house injection moulding: Any company producing its preforms itself instead of buying them on the market is no longer dependent on suppliers and also saves transportation costs and storage space into the bargain. Elaborate quality and hygiene checks that would otherwise be needed upon receipt of preforms are also no longer necessary. Yet another benefit is better preform quality because surface scratches caused by packaging and transport are reduced.
The Prefero injection-moulding system is suitable not only for new machines but for existing lines as well. Ultimately, it results in a production operation that scores highly in regard to security and reliability, continuous quality monitoring, low energy consumption and minimised packaging weight.
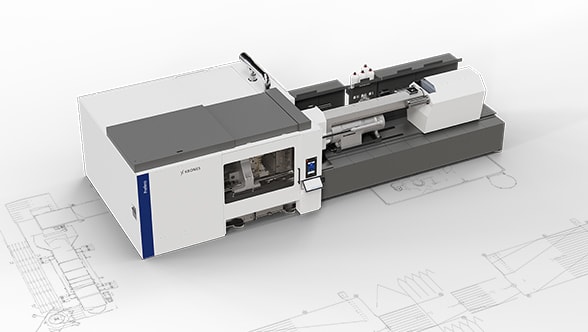
Energy-efficient production meets cost-saving preform design
Prefero uses around 20 per cent less energy than comparable machines and provides complete transparency, thanks to its visual display of energy consumption levels in real time. The application-specific HMI scores highly with its smart operator control options and simple start and stop functions. With just four soft buttons and a touchscreen in new design, the control panel offers access to all important device parameters. The voltage and frequency stabiliser (Cycle Guard), an optional extra, reduces the system’s susceptibility to short power cuts: Restart can be triggered within three instead of the customary 50 minutes.
Important aspects to be considered in packaging development are the preform design, the neck finish and the closure. The team of experts at Krones leave absolutely nothing to chance here because even the tiniest of adaptations in the configuration developed can make quite a difference. Specifications can be modified to match the tailormade in-house production operation, thus opening up potential for further reductions in packaging weight. The optimum stretch ratio improves a bottle’s characteristics in regard to top load, thermal stability, burst pressure and CO2 impermeability. It is a matter of mathematics, as Jochen Hirdinia explains: “One gram of material saved per bottle, calculated for 48,000 bottles and 6,000 hours per year, results in cost savings of more than 316,000 euros. That is only one of many sample calculations confirming Prefero’s cost-efficiency and sustainability in black and white.”