Thought through to the end
In order to considerably speed up the conversion process as a whole, KHS has not just simplified the individual work steps involved but also the concept governing the entire procedure. “We started out by analyzing how the operators work,” says Arne Andersen, stretch blow molding product manager. “On this basis we then considered how all tasks could be made easier and organized as perfectly as possible - paying particular attention to the ergonomics. Magazines were thus installed that stop the operator having to repeatedly abandon the machine to fetch and carry change parts, for example. We also replaced the grippers to reduce the number of screws that need to be loosened. At the same time, newly developed mandrel heads are now used that can be simply removed by pressing a release spring. This process used to be much more complex.”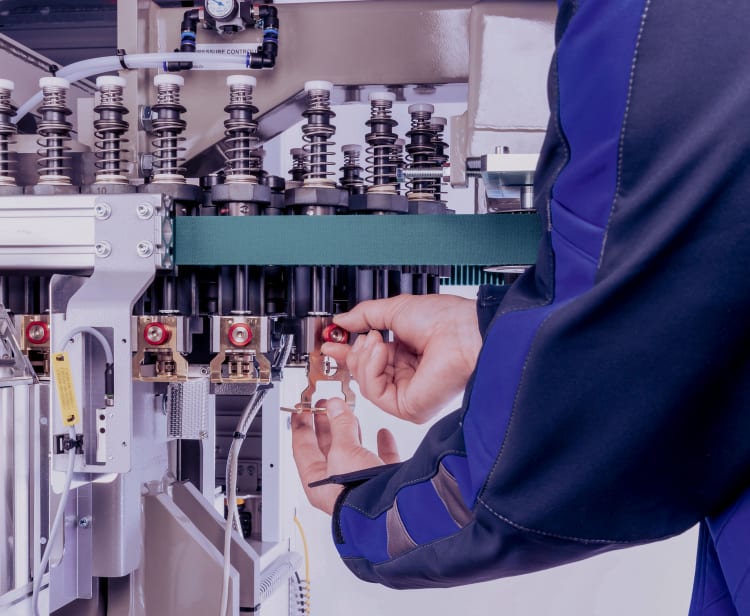
Step 1 shield changeover (source: Jörg Schwalfenberg)
In this case, KHS consciously went for an approach that thought all of the specific processes through to the end based on actual customer requirements, Andersen emphas. “We aimed to achieve the best possible improvement within the shortest possible time.” KHS managed both: thanks to the simple neck change, the time needed for two operators to convert the KHS InnoPET Blomax16 stretch blow molder, for instance, has now been cut by a good two thirds to approximately just 86 minutes - including the preform infeed. As the PET bottles in a block like the KHS InnoPET BloFill are held and conveyed by their necks throughout the entire machine, not only the stretch blow molder but also the filler has been developed further in order to shorten conversion times. The capper was one particular area of focus, where the cone responsible for lifting and closing the bottles needs to be replaced manually. No conversion is required regarding the screw cap, however, as there are two cap feeds - one for each neck diameter in the respective format.
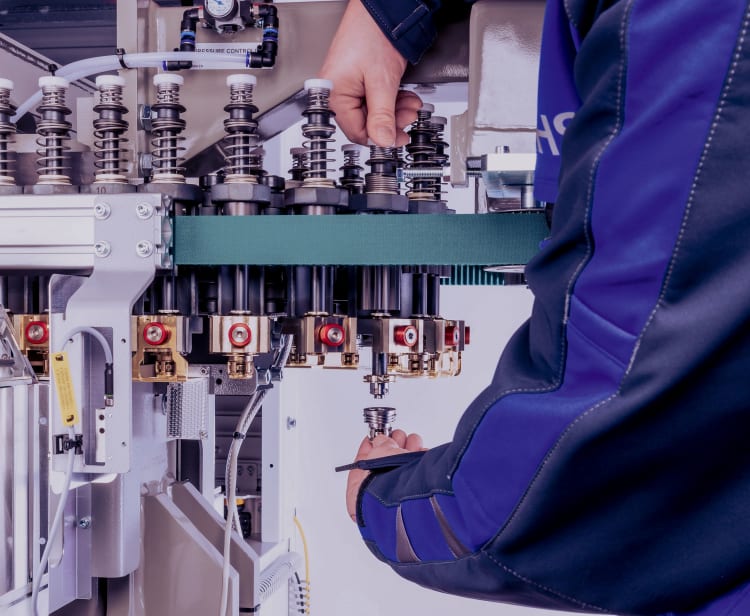
Step 2 mandrel head changeover (source: Jörg Schwalfenberg)