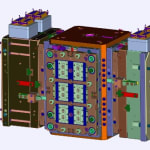
The special feature is that eight bottom and eight top parts are injected for each parting surface. In the 90° position transverse to the longitudinal mold axis, a handling system fully integrated in the mold removes the upper parts from the mold and screws these directly onto the bottom parts which remain in the cavity for this process step. Beside the compactness, another advantage is the system's excellent assembly precision and the related high production availability. It is always parts from the same cavities which are mounted against each other. The electric handling system designed and built by Foboha is programmed via a specially developed Foboha operating unit.
The actual product is a two-part screw top which, when closed, can hold a UV-sensitive powder, for example. As soon as the cap is opened, the powder trickles into the bottle and dissolves in the liquid below.
The second stack turn mold with all-electric drive runs at the Arburg booth in hall 13 on an Allrounder 720 A with 3,200 kN clamping force. The injection product is a two-component cap for carton packs (juice pack).
The 12 + 12-fold pilot mold is the basis for a high-cavity serial mold, designed specifically for the production requirements of mass-produced parts. The cube guide in the patented Foboha turning unit in which the mold is held top and bottom, is an important element of the system to guarantee the fastest possible cycle time with lowest mold wear and tear.
To ensure that the moldings stay freely movable, two incompatible materials are used for this cap.
Both for the pre-moldings and the finished parts, Foboha uses the proprietary hot runner system developed specially for high-cavity molds, with an open hot runner system used for the pre-moldings and a needle shut-off mechanism used for sheathing in the second station. The advantage of the proprietary system is the perfect design of the hot runner to match the high demands of this application.
The fully functioning and movable moldings can be inserted directly into the carton pack without any post-assembly work.