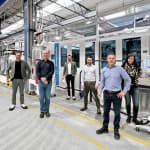
"ColorForm technology holds great potential for a lower CO2 footprint in the production of components with a finished multifunctional surface," explains Michael Fuchs, Global Application Owner Surface & Lightweight at KraussMaffei. Now the technology once more demonstrates its strengths at TECHNIPLAS, the well-known provider of sophisticated plastic components for the automotive and plumbing industries. In Treuen, Saxony in the Vogtland region, a KraussMaffei MXW 1000 ColorForm system for the series production of components with a transparent surface has been put into operation.
Process expertise and quality awareness are the keys to sustainable production in the automotive industry. The wealth of experience of Techniplas as the user and KraussMaffei as the provider of injection molding technology and PUR/PUA processing systems makes solutions possible that become increasingly more significant these days. ColorForm, that is, the ingenious fusion of injection molding technology and surface finishing with polyurethane in a single process step, is one such solution.
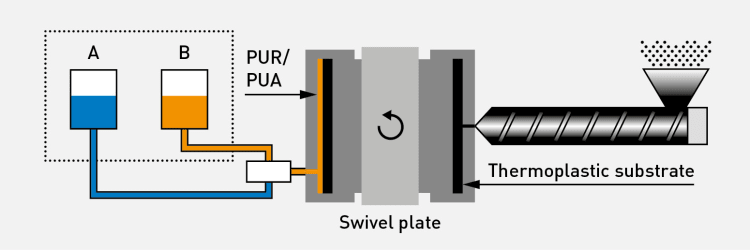
Schematic representation of the PUR/PUA flow-coating in the mold.
ColorForm: Coating right in the mold
The ColorForm process is based on a combination of injection molding and polyurethane processing. The tried-and-tested multi-component injection molding procedure is the foundation of this process. What is special about it: After injection molding of the thermoplastic mold base body, this body is flow-coated with polyurethane (PUR) or polyurea (PUA) as the surface material in a second cycle.
The RimStar Flex ColorForm reaction process machine, which was designed specifically for this process, and the mixing head feed the surface material (PUR/PUA) directly into the cavity. "RimStar systems take up very little space and meter even small amounts precisely and at a high clock frequency," explains Philipp Strasser, Global Application Owner RPM & Automotive at KraussMaffei.
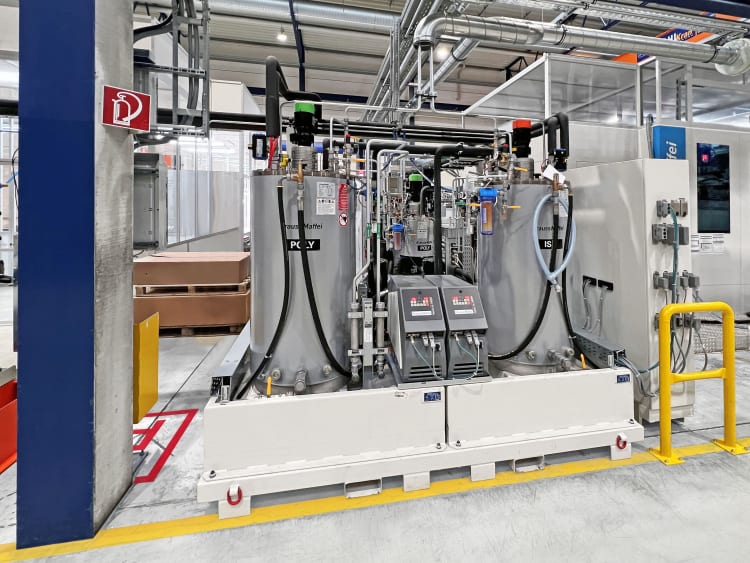
KraussMaffei supplied both the MXW 1000 injection molding machine and the RimStar Flex mixing and metering machine, including mixing heads for efficient production of components with a polyurethane surface.
Transparency with depth effect
"On this system, parts are produced in the injection-compression molding process. To obtain a special depth effect, a premium-quality, transparent PUR surface is applied to these parts," explains Toni Luckner, Process Developer in Treuen (Vogtland). "One more system for the project will be put into operation in the first quarter of 2022."
"Our customers, large OEMs from the automotive industry, have stringent requirements regarding quality. There must not be any deviations greater than 0.2 mm on any part of the transparent component. Using the MXW 1000 in combination with the RimStar Flex for PUR metering, we fully meet these requirements," says Luckner.
Techniplas has had positive experiences with the ColorForm technology from KraussMaffei for many years now. At Techniplas, the technology is called "ColorFuse". The company currently has four ColorForm systems in Treuen and one in Rüti, Switzerland. This system has been manufacturing ColorForm parts in series production since 2016.
In addition, their in-house TechCenter in Treuen operates two more systems.
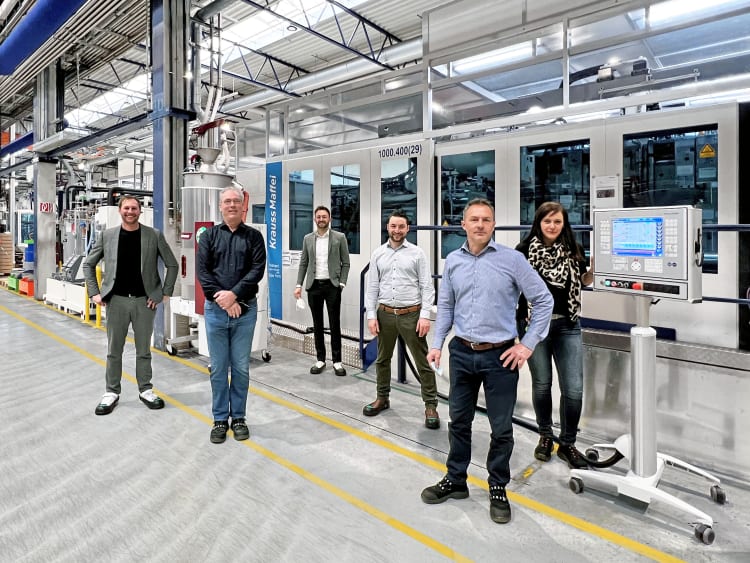
Mission accomplished: Employees from Techniplas and KraussMaffei are happy about the successful commissioning of the MXW 1000 ColorForm for the production of smartbars for the automotive industry. (from left: Peter Giessmann (KraussMaffei), Eric Jan Frijters (Techniplas), Philipp Strasser (KraussMaffei), Michael Fuchs (KraussMaffei), Rene Rudolf (Techniplas), Sarah Seidel (Techniplas))