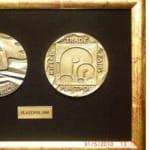
The last few years have seen a lot of energy focused on the realisation of wood-plastic composites (WPC), even by world famous leading companies, often aiming to bring the attention on its innovative aspects.
But up to the present day and in spite of all the efforts, the issue about WPC did not satisfy all the expectations. In fact, the physical and mechanical characteristics were improved but to a great disadvantage: very high specific and linear metre weight values due to the need to increase the profiles thickness, making the product very expensive and non-competitive.
Friul Filiere SPA realised an alternative and innovative technology that can avoid this inconvenience, as it allows the extrusion of a lighter PVC-WOOD composite through a closed-cells expansion system.
The FFC (Foam Fiber Composite) as it is named, introduces notable advantages: the most important is the substantial reduction of the end product cost, in fact it maintains the physical and the mechanical characteristics but has a very low specific weight.
To reach this result, Friul Filiere has developed a complete know-how that guarantees the entire production process, with respect to the following consecutive stages: drying of wood flour, transportation of raw materials, dosage, mixing, extrusion. Not least, the customer can also refer to the recipe of the compound that will be extruded.
The wood fiber drying plant is placed at the head of the production process and is necessarily synchronous with the operations of the rest of the plant; in fact, being a highly hygroscopic material, it can not be stocked but must instead be used batch over batch.
This plant consists of a hot air generator, a volumetric loader, a drying chamber, a air-solid separator, all controlled by a microprocessor previously set and programmed according to specific production needs.
Transportation, dosage and mixing are personalized to meet the needs of these raw materials which are characterized by a very low appearing density and a high resistance to flow.
A further characteristic of the know-how is the design and the realisation of a single screw extruder producing a finished profile directly from the dryblend, without having to go through the compound granulation process.
This is a series of 28D single screw machines with degassing system, volumetric dosage device and a screw designed for loading and plastifying low-appearing density materials.
Finally, the formulation is the result of a new research aiming to identify raw materials such as wood fiber with controlled dimensional stability, dried during the process itself until it reaches a humidity level of less than 2% with correct stabilisation and lubrication of the PVC that fluidizes the compound and covers the fiber.
Not least, a mixture of exo/endothermic chemical expanders that are not inhibited by the presence of the natural fibers, allows a closed-cell expansion and ensures a product with a smooth and rigid surface and an internal mass expanded with microcells, bringing the specific weight to levels such as 0,6/0,7.
The quantities of the basic elements contained in the compound may vary from 50% to 75% in the case of PVC and from 25% to 50 % in the case of wood flour. The compound presents high plasticization flexibility allowing it to be used on both single screw and twin screw counter-rotate extruders without having to go through the granulation process; it can also be mixed on standard PVC turbo-mixing plants. The equipment that completes the plant is also designed and realised by Friul Filiere SPA and is the heart of their technology.
As wood fibre extrusion is a low-speed process, both single or twin strand equipment can be realised to increase the productivity, mostly advised when processing medium-small profiles. FFC technology products have excellent physicotechnical characteristics and, thanks to their very low specific weight and internal porosity, can be mechanized on the same machines used for wood processing, planing, milling, gluing, veneering, etc.
Extruded profiles find varied applications in the field of construction and of furniture. Excellent profile stability, fire proof, highly competitive if compared to plastics but also to wood, high productivity, low cost.