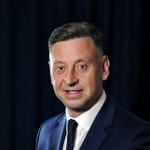
Poland generates ca. 110–130 million tonnes of waste every year. In 2018 it was 128 million tonnes of which 10% was municipal waste. Compared to the EU average (486 kg) and other EU countries (e.g. Denmark - 781 kg, Germany - 633 kg or Luxembourg - 607 kg), Poland has one of the lowest rates of municipal waste generation per capita (325 kg) (Eurostat, 2020). The problem, however, is the low level of recycling. In 2018 only 57% of the municipal waste collected was intended for recovery, of which 26% was subjected to mechanical and chemical recycling and 23% to energy recycling. The structure of municipal waste is dominated by: biodegradable waste (26 kg per inhabitant), mixed packaging waste (15 kg), bulky waste (14 kg), glass (13 kg), plastics (9 kg), paper and cardboard (7 kg).
Plastics are the third largest stream of mixed municipal waste (14%), immediately after bio-waste (which accounts for nearly 20%) and the segment of paper and cardboard (14.5%). Plastics constitute about 10% by weight and 40% by volume of household waste. Although the amount of municipal waste collected selectively has increased (in 2005 it constituted 5% of municipal waste collected while in 2018 it was 29%), but the recycling of plastic waste is largely based on easily collected waste from commercial networks and transport (Statistics Poland [GUS], 2019).
We talk about the history of recycling in Poland, the current situation and the opportunities and concerns of the industry with Tomasz Mikulski, CEO of ML Polyolefins, a Polish recycling company.
Mr President, the company you run has been present on the Polish market for 20 years. Please tell us what the beginning of recyclates production was like for you.
We started in 2000, but as a trading company for packaging and supplying waste to companies that needed it for processing. We started producing regranulates in 2006, when we set up our first recycling line. This allowed us to produce 70 tonnes of polypropylene regranulate per month. The beginnings were difficult, the crisis came in 2008 and demand for materials was much lower. However, we successively carried out further investments, developing the machine park and building our position on the market.
Did you already know then that recycling would be such an important part of the economy?
At the beginning, my job involved a lot of travelling and visit to western companies dealing with selective waste collection, thanks to which I could gain knowledge and experience. I was convinced that it would be possible to transfer Western models to Poland and improve waste management in our country. At the same time, the approach to waste was changing. We started to see it as a valuable material. We knew that this was an innovative action and an investment in the future.
What was the processing of waste into raw material like in the early days of the recycling industry in Poland?
Of course, in terms of material, in the early days, recyclate was very different from virgin plastics. However, there were many products that could be successfully made from regranulate, and the main reason for using it at the time was the economic factor. Over the years, awareness of recycling has increased among consumers and companies have developed technologically, so that the quality of recyclates is now very close to that of virgin materials. Now the added value for a product is the fact that it has been made from recycled materials.
What is the state of the company today, what do you specialise in?
Our speciality is the production of polypropylene regranulate. The production capacity of our plant is constantly growing. In 2020, we set up a fourth recycling line and now have a production capacity of 25,000 tonnes per year. Since 2015, we have also been producing compounds based on recyclates. For filling we use minerals and chemical additives. Thus, we are able to develop an application individually adapted to the requirements of our customers. In addition, we have modernised the laboratory. This allows us to monitor the technical parameters of the material in real time, and our products are characterised by high quality and reproducibility, so that contractors use them in more advanced details.
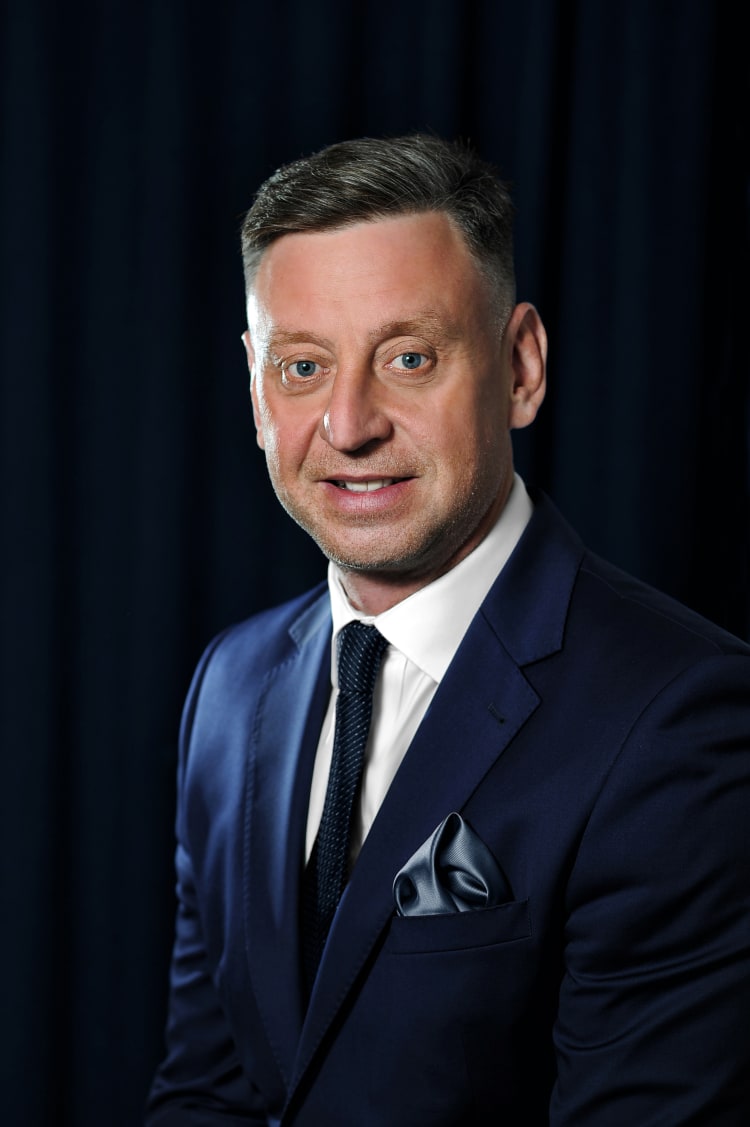
Tomasz Mikulski, CEO of ML Polyolefins. Photo: Karol Bannach