Online support, remote service, augmented reality – the functions are now already widely used. What are your achievements in this area?
Digitalization is one focus of ENGEL's development work. Every year, we invest tens of millions in digitalization. There have been massive changes, particularly in the Service Division, in recent years. Numerous newly installed injection molding machines are already online, and more are coming online all the time. The rising number of digital applications will automatically cause machine connectivity to grow. Covid-19 has accelerated this development. After all online support and remote maintenance are key to ensuring productivity and delivery capability, even in a crisis.
During the pandemic, when on-site service calls were not possible to the usual extent, our experience with video telephony as a component of our online support was excellent. Our new e-connect.expert view offering grew from this. Where the ENGEL service technician in classic online support has access to the injection molding machine's control interface in real-time, the new web application relies on video to provide additional information on the status of the machine components and the injection molding machine's environment. Some three quarters of all urgent service cases can be resolved remotely in this way. Troubleshooting times are reduced by 70 percent.
Video telephony is supported on both smartphones and tablets and using augmented reality (AR) glasses. The only pre-requisite is an internet connection.
Some of ENGEL's customers have already started working with AR glasses, and there is a general interest in the new technology. The advantage that AR glasses offer is that both hands remain free to work on the machine. Besides this, additional information supporting the collaborative work can be displayed in the form of text, animated objects or short video sequences.
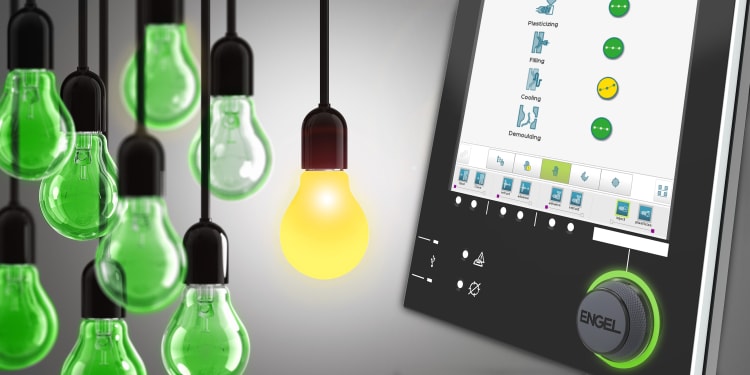
We are also seeing the rapid development of AI. This is particularly noticeable in the social sphere, although we often see side-effects of this development as well. But let's stay with our business. What is the role of AI for injection molding processes?
Artificial intelligence is also opening up new opportunities in injection molding. The first application for the injection molding machine is iQ process observer by ENGEL, which sees us move further towards the self-controlling injection molding machine. We collect anonymized and generalized data from analyses provided by customers who explicitly gave us their approval for this. Accordingly, we can draw on the accumulated experience of a broad installed base for the further development of iQ process observer and for artificial intelligence training. Our customers are benefitting from the continual improvement of the software.
Finally, I would ask you to play the role of a visionalist. What will the injection molding technology sector look like in 20 to 30 years?
The processes will be smart and transparent. In this way, we can ensure the extremely economical use of energy and raw materials and keep plastics in circulation.
Until then, the main thing is to network the companies in the plastics industry even more closely along the entire value chain.
Applications such as ENGEL e-connect.24 for remote maintenance and online support, are primarily implemented on vertical platforms today. What vertical means here is digital mapping of a system or production cell within a single stage of the value chain. This "digital twin" describes the system and its behavior based on data and lays the foundation for optimization.
Through a transition to horizontal platforms, which is being actively promoted by ENGEL and other companies in the plastics industry, we can network these applications along the entire value chain and exchange information and data across enterprise boundaries. This benefits the circular economy and we will no longer have to downcycle materials, but can focus on genuine recycling or even upcycling. For example, a digital watermark applied invisibly to packaging enables targeted sorting of plastic waste, resulting in single grade, high-quality recycling. The watermark identifies the material, the packaging manufacturer and the processing method. The data is available to all participants and users of the horizontal platforms in order to be able to control and tune the recycling process, and the processing of the recycled materials downstream, for maximum resource efficiency. In this way, we are shaping a sustainable plastics industry in collaboration with our customers and partners.
Jacek Leszczyński