CO2-neutral from the outset
GID has set up an intelligent collection system for packaging waste made of EPP/EPE, which is both voluminous and very light. To recycle the packaging as efficiently as possible and also reduce CO2 emissions, the company has established collection points throughout Europe where the packaging waste is first compacted. As a result of this process, one truck can carry the amount of material that would normally fill 22 vehicles.In Eschwege, forklifts feed the palletised and sorted waste directly into the shredders. The VIZ 1700 processes baled packaging residues, production waste and purgings. These bales have maximum dimensions of up to 1,200 x 800 x 500 millimetres. Stretch films, ropes and coarse nets are also processed. The smaller VIZ 1300 shreds waste up to a maximum of 1,200 x 400 x 400 millimetres in Eschwege. The input material, consisting of various plastics, is hardened and contamination-free. Vecoplan also supplied flat belt conveyors with a small intermediate buffer that transport the shredded material to the extruders. Neodymium magnetic head drums separate metallic impurities that are already magnetised. “We were able to permanently set parameters like ram behaviour and speed without having to change them during operation,” explains Philipp Güth. In some cases, the systems run at a speed of only 25 per cent; the previous shredder ran permanently at 100.
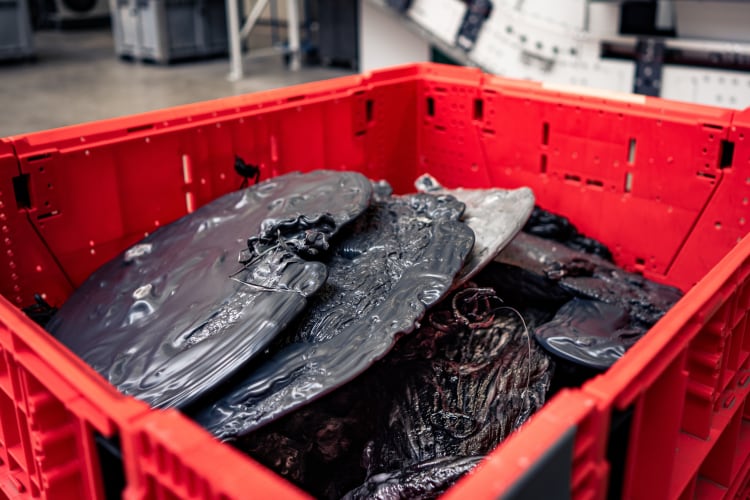
The input material includes purgings (post-industrial waste) …
Risk of accidents averted
Another important aspect for Matthias Henning is also the safety of the machines. “With our previous shredder, accidents kept happening during maintenance,” he reports. “The main reason for this was that we had to turn the rotor manually when we were changing the cutting tips.” Thanks to the HiTorc drive, the VIZ can move the rotor at low speed to the appropriate maintenance position. There is a special mode for setting the cutting gap perfectly and safely outside of the machine. All the maintenance work can also be carried out ergonomically thanks to the hydraulically operated, swing-open bottom flap. The concept of bolted tool holder plates with variable cutting tip s also means that rotor changes are no longer required.Sophisticated digitalisation concept
The two shredders are equipped with the Vecoplan Smart Center (VSC), and the intuitive VSC.control operating panel is integrated into this powerful digitalisation concept. The panel serves as a communication medium for modern control and a direct link to Vecoplan. The machine is networked with the help of the VSC.connect. The VSC.connect also provides online access to additional services such as key performance indicators, remote service and a media database.
“We can use it on our iPads to examine the condition of the shredders and intervene on ourselves if necessary,” says Henning. “That's especially important on weekends when neither I nor the plant manager are present.” Key performance indicators include not only throughput per unit time, but also power consumption. This provides information about how efficiently the material is being processed. With this option, GID can present the actual costs to its customers even more transparently –
and the temperature from the output can be continuously measured with the VSC. A rotor which is too hot can cause some plastics to melt and this in turn causes the components to stick together. In the past, this very often led to unplanned shutdowns during continuous operation. The GID managing director is delighted: “Thanks to the Vecoplan Material Cooling (VMK) system, we can now control the temperature continuously and cool it down only when the process requires it.” The plant manager can also remotely connect to the machines at any time. A camera gives him a view of all the sensitive areas. This minimises downtimes.

… as well as stamping grid residues (post-industrial waste) pressed into bales.