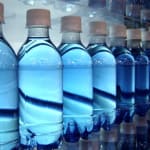
This is an annual increase of 5.6%. The key applications for PE are packaging at 69% and infrastructure at 11%, while for PP the percentages are 43% in packaging and 11% in automotive and appliances. This market information was discussed at the AMI conference on Polyolefin Additives, which took place in October 2011 in Cologne, Germany.
The leading material suppliers conduct extensive research, like Borealis Polyolefine. Molecular structure, processing and additives all affect properties. Stabilisers and modifiers need to be compatible with the polymer, have high solubility and low migration rate and meet all safety standards. The range used in polyolefins includes antioxidants for processing and long-term stabilisation, UV stabilisers, antistatic, slip agents, nucleating agents, flame retardants, impact modifiers, lubricants, foaming agents, fillers and reinforcements.
It is also important that recipes take account of synergistic or antagonistic effects of additive combinations, for example hindered amine light stabiliser (HALS) is antagonistic to sulfur antioxidants. Some additives have dual effects, for example nucleating agents can improve thermal stability, perhaps because of the increase in crystallinity. Fillers are particularly important as the chemical nature, particle morphology and surface treatment can all affect material performance and additive interaction.
Analysis carried out by Basell Deutschland a LyondellBasell Company, has shown that polymers now account for around 19% of the materials in cars, which amounts to around 170 kg per vehicle and 60% of this is PP. The industry trends are towards manufacturing in low cost regions and light weighting, while cost dictates the types of materials used in different applications.
For example, in high end cars there wil be foam-backed skin foils, in the middle range there is a plastic surface with soft-touch paints and at the lower end the plastic is uncoated. Basell Deutschland has developed new soft touch PP compounds for automotive interiors which meet the latter requirements. The base resin, Softell, has a very fine dispersion of elastomer particles in PP giving low gloss and high Shore D properties (low scratch and mar), whilst maintaining processability in injection moulding. As it does not require coating it has the potential to reduce costs.
BYK Chemie has developed additives for reducing odour and fogging in automotive applications. During extrusion the carrier releases active substances, which form microfoam under the raised temperature and shear stress. In this process the volatile organic compounds and odour components are wetted. Downstream the microfoam collapses and these components are released in degassing of the extruder. Thus BYK-P 4200 acts as a sort of stripping agent.
In packaging, Danisco has efficient anti-fogging solutions for both PE and PP, which prevent the formation of water droplets on the inside of the film (this is also used in agricultural applications). Chemically-modified fatty acids are used, with a tailored polarity to control migration. The antifog works by reducing the surface tension at the water/polymer interface: in effect the condensed water forms a thin continuous film and there is no loss of transparency. If the antifog is to be used in a complex multilayer construction then it needs to be added to several layers, because the sealing layer where it needs to be active is usually only around 8 microns thick.