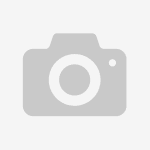
Graham Engineering Corporation, the York, PA, USA-based manufacturer of extrusion blow molding equipment, will exhibit a rotary MINI Wheel blow molding machine at NPE 2009, from June 22-26. On display will be the rotary portion of the blow molder, along with a complete 5-material, 6-layer extruder system and controls.
Due to customer requests, Graham has recently expanded the MINI wheel line from 12 stations to include 9 and 10 station versions. This gives its customers the option of running larger containers than those that could be accommodated on the original 12-station MINI wheel.
The MINI Wheel is a compact system based on its popular Wheel blow molding systems for high production environments, a technology it has been providing since the 1960s. - The Graham name is synonymous with Wheel machines and Wheel machines are synonymous with mass-produced packaging - notes David Yenor, Vice President for Global Business Development. - The MINI Wheel represents a breakthrough for smaller molders looking to dramatically increase throughput. This opens up the market — Graham rotary wheel technology is now available to mid-sized blow molders who previously did not have quantities to justify the purchase of a Graham Wheel machine.
The MINI Wheel is small enough to ship in a standard freight container. Like all Graham Wheels, it combines continuous, rotary motion, upward extrusion, and bottom takeout. Graham developed the MINI Wheel specifically to produce co-extruded plastic containers in high growth areas such as flavored milk, organic drinks, coffees, teas, nutraceuticals, yogurts, probiotics, packaged fruit, smoothies, fruit juices, drinks with fruit chunks, specialty milks (Lactose reduced, Omega 3, Acidophilus), as well as ketchup, jellies, salsa, and other oxygen-sensitive food products that have to be packaged in barrier plastics.
With the introduction of the MINI Wheel, molders who need up to 12 cavities of production now have a superior processing alternative to a five- or six-parison, double-sided shuttle machine. Advantages of the MINI Wheel are numerous. The MINI Wheel has only one flowhead to control. The parison is captured on both ends, between the preceding mold and the flowhead, and is thus always the same length. As a result, there is no possibility of parison curling or movement due to static electricity or air currents. This enables the operator to more accurately “program” the thickness of the neck, sidewall, shoulders, or bottom of the bottle.