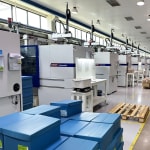
Design is his passion, and the products show it. Tomaz dos Santos is the owner and CEO of Thomriss, a major Brazilian manufacturer of make-up packaging focusing on eyelash and eyebrow mascaras. His daily challenge: producing high-grade surfaces sustainably at competitive costs. Injection molding system supplier Wittmann supports this effort with machines, automation, auxiliaries and extensive application technology expertise.
Tomaz dos Santos is particularly proud of the large clean-room area at the corporate headquarters newly constructed ten years ago in Lençóis Paulista, just under 280 kilometers north-west of the São Paulo city. “Quality is our top criterion”, the CEO explains to us during our visit to the production plant. On the table inside the large, bright conference room, a great variety of packaging items are displayed, such as lipstick cases, eyelash and eyebrow mascaras, makeup jars and dropper bottles for liquid preparations. The company’s product range includes more than 50 different types of packaging. For injection molding production, this is an enormous figure. For it must be remembered that one lipstick and facial stick alone requires more than five different molds, and every product can be ordered in innumerable variants. All products are available in a very broad range of different colors, and with color gradients as well. Many packaging parts are printed on, metallized or painted. The main eye-catchers are the anodized lip gloss and eyeliner packs with their particularly elegant glamor.
“This can only be achieved by highly accurate and perfectly clean production”, explains dos Santos. Even the tiniest dust particle or slightest unevenness would become clearly visible after metallizing and thus cause scrap. The prerequisite for perfect surfaces is high precision in injection molding. 44 injection molding machines with clamping forces ranging from 120 to 240 tons are installed in the injection molding hall. Nearly all of these are SmartPower machines from the Wittmann Group. With 65 per cent of all parts produced, injection molding processing takes up the lion’s share of manufacturing activities at the facility.
“The SmartPower injection molding machines offer extremely precise machine movements together with strong dynamism and high efficiency” says Cássio Luis Saltori, Managing Director of Wittmann Battenfeld do Brasil. “With these attributes, the series is predestined for use in the particularly price-sensitive production of upmarket cosmetics packaging.”
Their drive-on-demand technology combines fast-responding servo motors with powerful constant displacement pumps to enable extremely fast and simultaneously precise machine movements with minimal energy consumption. The KERS energy recovery system produces an additional energy-saving effect by transforming the kinetic energy from deceleration processes into electrical energy. The power derived from this can then be used for functions within the machine such as barrel heating.
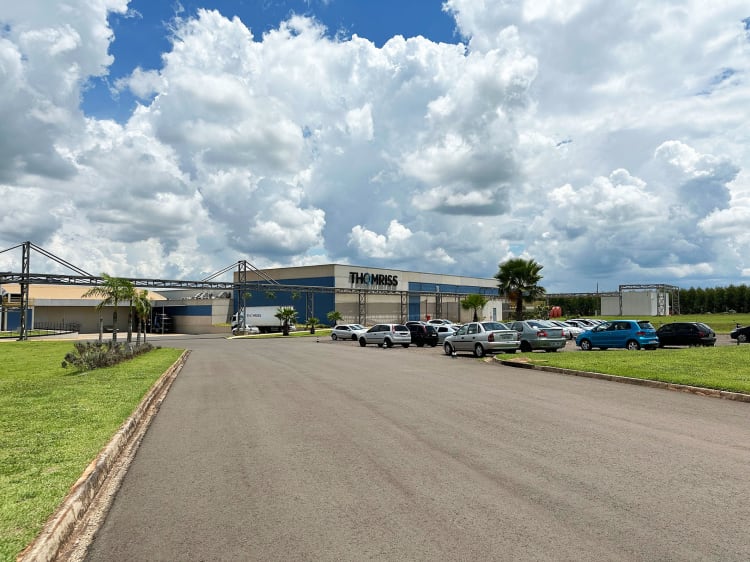
Consistent quality standards to minimize production costs
The cooperation between Wittmann Battenfeld do Brasil and Thomriss has long since become friendship. Tomaz dos Santos and Marcos Cardenal from Wittmann Battenfeld do Brasil have known each other for 33 years. Tomaz dos Santos founded his company and purchased his first injection molding machines in1990. Although impressed by Wittmann Battenfeld from the very beginning, the company first invested in injection molding machines from a Chinese supplier. For cost reasons, according to the CEO. But the quality did not convince him. This is why now only machines from the Wittmann Group are admitted to the plant. Due to their extremely high process stability and quality consistency, they have proved less costly in the end. Not to forget: the application technology support given by Marcos Cardenal and Cássio Luis Saltori. “My family always says: Tomaz, your second name is Battenfeld,” dos Santos tells us with a twinkle. “That has almost become a love relationship between me and my technology supplier.”
Since 2008, the Battenfeld brand of injection molding machines has been a part of the Wittmann Group. Witmann is the only supplier on the market able to offer turnkey solutions covering the entire injection molding process, including raw material preparation and feeding, as well as injection molding, automation and mold temperature controlling, inline recycling and digitalization. Tomaz dos Santos fully exploits this advantage for his company. The whole range of auxiliary equipment for drying, handling and dosing of the plastic granulates comes from Wittmann, as well as the linear robots for demolding and depositing of the molded parts. The automation systems are becoming more and more important for Thomriss in view of the rising quality and efficiency standards.
PET in more and more applications
“Wittmann is a development partner for us,” dos Santos emphas. “Whenever we are facing new challenges, we get together to develop a solution. I can always rely on Cássio and Marcos to find the best possible deal for us.” Such as for the dropper bottle lid with an integrated pipette made of two different materials. TPE is used for the flexible dome, while the screw top consists of polypropylene. Both com-ponents are produced in multi-cavity molds and directly assembled at the plant im-mediately after injection molding. Following extensive testing, the two development partners jointly selected the materials and optimized the process. “With this solution, we are very flexible and inexpensive”, says dos Santos.
Wherever permitted by the required functionality, Thomriss follows a strict mono-material strategy. “Sustainability ranks very close to the top of our customers’ priority list. In the cosmetics sector, sustainability of the packaging is an important purchasing argument”, explains dos Santos.

This is precisely why a material which is relatively new for Thomriss is rapidly entering its product portfolio: PET. “PET has many advantages. Packaging items made of PET offer transparency, high rigidity and durability. The decisive factor for us, however, is recycling. For this material, a closed cycle already exists. So, we design more and more packaging items to be made of PET and go the PET way in high-volume applications as well.”
Among the products displayed on the conference table, we find several specimens of innovative cosmetics packages consisting of PET and recycled PET. For example, lip gloss packs, which are running off the clock-out belt of a SmartPower machine on the day of our visit, and which we meet for a third time shortly afterwards in the clean room for surface finish.
New central system improves efficiency in materials handling
One of Thromriss’s major customers is Boticário, for example, a large producer of make-up, care products and perfumes, for whom packaging products are produced in Lençóis Paulista.
The modern facility offers 16,000 square meters of floor space, the production is continuously being extended and modernized. In the near future, a new, large central system from Witmann will be installed for granulate drying and material feeding. This step will also contribute to a further increase in efficiency and sustainability.
Tomaz dos Santos has many more plans for the future, and the family pulls together. With his daughter and son, the second entrepreneurial generation is already in the starting blocks.