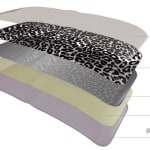
Unlike traditional production methods, this novel technology involves cutting the finished frames from a single, curved preform, thus omitting the machining and finishing steps after injection molding. The preform is made ahead of time from multiple functional layers - the base frame made of TROGAMID, the adhesive and coating layers, or the scratch-resistant film - and can be produced relatively quickly and flexibly, varying both the size of the preform and its radius of curvature.
Design variety with TROGAMID
IMPLEX wins customers over with easy handling, excellent productivity, and the ability to customize in a variety of colors, textures, and patterns. For eyewear manufacturers, the ability to implement designs even more quickly is a major advantage of the innovative technology.The innovation meets customer demands through its use of two material solutions from Evonik: TROGAMID CX9704 is a transparent polyamide used for the base frame - its pliability allows manufacturers to vary the shape of the product. The second structural layer, which is made with TROGAMID CX9711, has excellent processing characteristics and is highly resistant to chemicals.