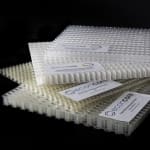
Experience in packaging
EconCore actively licenses its technology for the continuous production of thermoplastic honeycomb core materials, to companies around the world in various industry sectors. The advantage of being able to produce core materials with optimized performance-to-weight ratios, at high speeds, in high volumes, and with the lowest possible costs, has brought the honeycomb structure - once reserved for aerospace and low volume, less cost-sensitive domains - to mass markets.The early breakthroughs for EconCore’s technology were in packaging, with the company’s first licensee in Japan (Gifu Plastics) focusing on lightweight high-performance solutions made with polypropylene honeycomb-cored sandwich panels. Over time, the advantages offered by an efficient material geometry produced with an efficient technology have attracted many more new users focusing on packaging - and other sectors too - with EconCore’s licensing footprint now also including automotive, transportation, building and construction, and PP core materials for composites.
Packaging remains the cornerstone of EconCore’s licensing business, with the largest share of licensing dedicated to applications in this sector. Building on this experience and the growing market share for honeycomb materials in packaging materials, EconCore technology is now a more attractive opportunity than ever for packaging companies as they plan new investments.
Foundations of performance
The honeycomb structure is recognized as optimal in terms of material utilization for performance. A comparison of the different core structures used today in packaging confirms this view. Consider the conventional fluted design (widely known as twin-wall corrugated), with its direction-specific structure: although rigid and strong in the longitudinal (machine) direction, these properties are much lower in the cross direction. Packaging materials made with a true honeycomb core structure have better and more directionally-balanced performance than the conventional fluted design - and they also weigh less.Cup-shaped core structures, also common in packaging, exhibit a more balanced bi-directional performance in general, compared to fluted structure. However, in terms of compression strength and weight, the true honeycomb structure significantly outperforms cup-shaped core materials.
Whereas the non-isotropic design of the fluted structure clearly explains the imbalance in performance, for cup-shaped structures the reason is due to the production process. During the forming process to make the cup-shape core, the material stretches severely and unevenly, leading to very thin walls in the cup tops and a reduction in mechanical performance. This is particularly acute for thicker packaging parts, as the stretching increases directly with thickness increase.
The true honeycomb core structure created by the EconCore process, with its hexagonal cells initially oriented horizontally and then folded vertically with adjacent walls all connected to each other, shows greater rigidity, a higher flexural modulus, higher flexural strength and higher compression strength. It is well known from aerospace applications that a hexagonal honeycomb is overall the best design for sandwich structures. With the EconCore technology, this core geometry is available for industrial packaging applications.