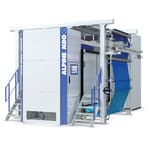
Hosokawa Alpine AG presents a further development of the Machine Direction Orientation (MDO) technology. The new generation of Alpine's MDO lines is equipped with a vacuum roll which optimises the production of high-quality oriented film: "We are proud to use our more than 20 years of experience in MDO technology for this further development. This will significantly improve the production of fully recyclable monomaterial films and contribute to the packaging solutions of the future", explains Dr. Holger Niemeier, board member and head of the blown film division at Hosokawa Alpine.
MDO technology is based on monoaxial orientation. It opens up the possibility of specifically adapting and improving the optical and mechanical properties of the end product. Barrier properties, optics or film thickness can be modified. Depending on the MDO design, the film runs over eight to twelve rolls, two of which are stretching rolls.
The second of these is now a vacuum roll with a porous surface. Due to the vacuum inside the stretching roll, the film is guided tightly against the roll. This significantly improves flatness and the MDO film is optimally prepared for lamination or printing.
The Hosokawa Alpine MDO technology is a crucial component in the production of high-performance mono-material composites made of polyethylene. This has a particular impact on the material cycle: until now, in order to generate certain product properties, composites of different materials were produced, which cannot be fully recycled.
Full-PE packaging solutions, i.e. films made from pure polyethylene composites, are a more environmentally friendly concept. These can be fully recycled after their original use and reused in the circular economy for end products without material loss. This combines sustainability and resource conservation. Hosokawa Alpine can already look back on numerous successful projects with partners, in which high-performance and resource-saving packaging of the future has been produced.
In the past, the patented Hosokawa Alpine TRIO technology ("Trim Reduction for Inline Orientation") has already provided significant material savings in edge trimming. In addition to this innovative solution, the new vacuum roller also reduces the neck-in by up to 70 per cent. Neck-in means the reduction in usable width due to the material being pulled apart. So the significant neck-in reduction saves further resources.
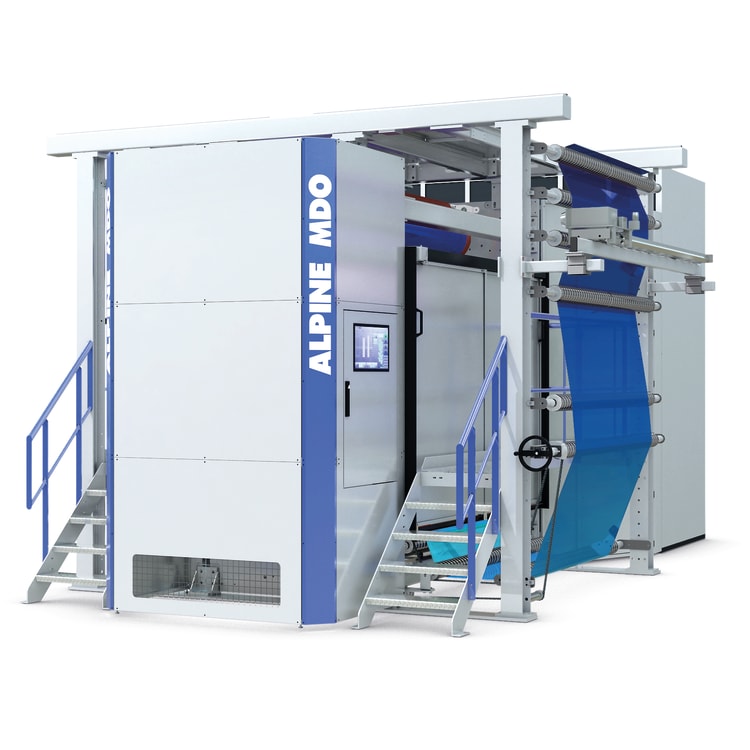