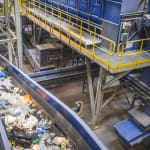
Digital technologies, whether used for traceability or identification in sorting facilities, have great potential for increasing the recycling rate of plastic packaging.
Material producers and chemical companies are working intensely on various projects and initiatives to create closed loops for plastics. Associations like the Alliance to End Plastic Waste, Circular Plastics Alliance, Global Plastics Alliance or the HolyGrail Project are conducting research into new technologies for the recycling of the future. Because there is one thing that industry, society, and governments agree on: Plastics are still being recycled in insufficient quantities. Of the 360 million tons of plastic produced worldwide in 2018, a mere 50 million tons were sorted for recycling. These were some of the findings of the “Global Plastics Flow” survey conducted by Conversio Market & Strategy GmbH in partnership with associations from the Global Plastics Alliance and other institutions. Of course, this issue doesn’t just affect packaging. But a large proportion of the 36 million tons of plastics that the survey found were not disposed of properly contains packaging waste. This is inconsistent with the idea of the circular economy, in which such great hopes are invested for the future. If an item of packaging has done its job and then ends up as waste, it should be regarded as a resource and if possible, re-used in a closed material loop. Accordingly, the end-to-end traceability of the material can simplify and optimise the management of the material flow. In this context, digital solutions will play a key role.
Traceability of material flows
With the help of digital tools, the Circular Plastics Economy Project aims to demonstrate, for example, how the energy and material flows of a recyclable material chain can be transformed into a circular economy. To this end, special system services are being developed with and for the plastics industry, including the producers of consumer goods and retail companies associated with it and the recycling sector. The aim is to boost both mechanical and feedstock recycling using advanced technologies and digital systems. This also includes digital tracking of materials and products over their life cycle, so that producers and recycling firms can make faster and better decisions about effective closed loop options.
The DiLink Project takes a similar approach. Technologies are being developed and infrastructures established that are designed to help exploit the potential to use recycled plastics. This is intended to rectify the problems of volume and quality associated with recyclates. These hindrances will also be countered by using digital tools like online trading platforms for plastic waste and recyclates, or digital process measuring technologies.
Easier identification of materials
However, as well as managing material loops, digital technology can also improve the results obtained in sorting facilities. Matthias Giebel from packaging consultancy Berndt+Partner (B+P) cites the HolyGrail Project as an example. The project was the overall winner of the Sustainability Award at the last Fachpack. For the project, renowned companies have joined forces to improve the sorting of plastics in recycling facilities using digital markers. “The currently still too low recycling rate in Germany is in part due to inadequate sorting efficiency,” explains Giebel. “There is a lot of confusion about contemporary packaging because of its material mix, i.e., the combination of different types of packaging,” says Giebel. Digital watermarks like that developed by Digimarc enable different categories of material to be identified and sorted efficiently. The US company’s technology is now set to allow the companies participating in the HolyGrail Project to better identify their plastic packaging in waste facilities so it can be passed on for recycling. “The aim is to obtain high-quality recyclate to replace fossil resources. Until now, for example, one of the few quantitatively important and reliable sources of high-quality PET has come from the recycling of PET drinks bottles, and these volumes are now being removed from this single-use system,” says Giebel. However, the demand for recycling material is likely to lead to shortages in future. The circular economy would then fail due a lack of recyclate. Low oil prices and the resulting drop in the price of polymer raw materials from petrochemical plants also have a negative impact on the competitiveness of recycling materials. Giebels points out that Germany already has an efficient recycling infrastructure. “Nevertheless, incentives need to be created for the recycling of plastics to overcome these teething troubles. This means a regulatory framework that would control the price of new products that are not recyclable (bonus-malus regulation),” he argues. In respect of the European Commission’s Green Deal, the B+P partner is nevertheless confident that policymakers have recognised the need to take action: “The Green Deal is aligned to the market economy and shows that sustainability can also be realised in an economic environment But it needs to go faster.” Only if recycling firms can plan ahead with certainty will they then also invest in the new technologies and consequently provide sufficient quantities of recycled plastics at competitive prices.
Thanks to their material properties, plastics are in fact ideally suited for recycling. The infrastructure and technologies are available, and as the many initiatives and projects show, the will to establish a circular economy is also there.