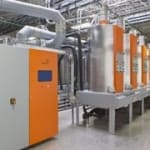
In April 2011, the last instalment of the equipment was delivered comprising of more than 500 Gravicolor gravimetric mixing and dosing units and over 1500 Metro material loaders. In addition, motan has installed 24 large external silos mounted on load cells which are linked to 48 fully automatic Metrolink material selection and distribution units to feed the raw material to the injection moulding machines.
Over 100 km of material feed-lines have been installed throughout the system. Material drying is performed with 16 Luxor dryers, each with a capacity of 2400 m³, and with 104 drying bins. The CONTROLnet control and management system ensures smooth and accurate operation and monitoring of these complex processes. The controls, which are Ethernet based, allow for the integration of drying, mixing, conveying and storage up to a higher-level visualisation.
The LEGO Group has been cooperating closely with motan-colortronic for the past 10 years. Detlev Schmidt, a sales director at motan-colortronic, led the initial discussions for the project in 2009. “We had already completed a project for LEGO in their Monterrey plant a year earlier. It was a central raw materials handling system with silos, storage, drying, material conveying and gravimetric dosing for more than 150 injection moulding machines.
Despite installation delays due to the swine flu in Mexico and volcanic eruptions in Iceland, we were able to complete the project on time,” Mr. Schmidt recalls. But the new project is bigger and more complex with over 700 injection moulding machines by the end of the expansion. Located in Monterrey, in the state of Nuevo Léon in Mexico, LEGO manufactures products for the North, Central and South American markets. The factory is in operation 363 days a year.
Jes Bladt, the senior director and production manager at LEGO in Mexico, explains that one of the most vital prerequisites for the company is extremely flexible and trouble-free operation, guaranteeing high quality and total reliability.
”We have to be able to totally rely on timely delivery of all bulk raw materials to each one of the injection moulding machines. Here, straight-forward and fast material and colour changes are essential. All of the gravimetric mixing and dosing equipment is mounted on movable frames adjacent to the machines.
This enables the highest degree of flexibility.” Following a colour/material change, the individual units are cleaned in a separate area, ready to be deployed again. An equally important subject for LEGO Mexico is the motan service. From their bases in Monterrey, Mexico City and San Diego, motan service engineers are able to be on site at very short notice, round the clock, 24/7.
To further ensure operational reliability, Detlev Schmidt explains the necessity for the vacuum technology. Each production line of about 25 injection moulding machines are supplied with virgin and regrind material through 2 side channel blowers. The blowers are turned on and off alternately to balance out the operating hours of the individual aggregates.
Velocis side channel blowers from Elmo Rietschle are used, Elmo Rietschle belongs to Gardner Denver, and as Mr. Schmidt points out, “they are maintenance free and low noise.” Also, the frequency-controlled blowers (via adjustments in the air volume) allow for a far gentler material conveying.
Detlev Schmidt further illustrates the new LEGO project by quoting just a few more details. “We have needed up to 20 installation technicians on site during the year to meet our deadlines. To transport all the equipment to the site, more than 50 large 40’ containers were required. The large outdoor silos were transported separately.”