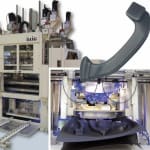
The universal forming machines of the UA-g series which are now all process-controlled provide a comprehensive, product-oriented variety of types and different equipment levels featuring different forming areas. In all of these sheet processing machines high precision and repeat accuracy is combined with high productivity, product quality and operating efficiency.
The innovative air ducts for ventilating and air condition systems in automobiles document, among other things, the efficiency and versatility of this generation of thermoformers. They meet demands in today's automotive engineering to a very high degree.
Performance feature of the process-controlled ILLIG UA-g sheet processing machines is the use of servo motor drives. The user benefits from a lot of advantages. Movements of individual functions can be performed faster with individual speed profiles adjusted to the respective process level. In total this results in shorter cycles and thus considerable increases in cycle speed.
This way thinner basic materials can be used (sheet or roll material) which improves efficiency. Moreover, energy consumption of servo drives, compared to pneumatic and hydraulic drives, is lower. The UAR 155g sheet processing machine, adapted for thermoforming of air ducts in the so-called twinsheet method, also makes use of this technological possibilities. Sheets sizes of 1.250 x 1.500 mm² can be processed on this machine.
Ducts suitable for guiding cold and hot air in vehicles must be heat resistant as lightweight as possible at the same time. They should dampen the sounds which usually occur during air flow, prevent formation of condensation water, be as flexible as possible for installation, and – last but not least – they must feature an often sophisticated, three-dimensional geometry for purposes of space-efficient installation.
All of these demands were realized with the process-controlled UAR 155g universal forming machine in the twinsheet method now in an especially efficient way: Two foamed PE materials are formed into two tool halves in the automatic thermoforming machine and welded together instantly. Precise punching of the welding seam contour is performed without mismatch in the same tool, so additional edge cutting is not required.
Drives of upper and lower table as well as loading of UAR 155g were adapted, among other things, for forming and punching of the twinsheet parts in the forming station. The loading device is equipped with a servo-driven double material transport with toothed chains for two material webs, servo-driven transport width adjustment as well as servo-driven height adjustment for upper and lower material transport. The foamed materials are drawn off by two rollers and processed. Thanks to the large forming area of the UAR 155g thermoforming machine long parts as well as large-area parts can be manufactured. The forming area can be used in almost any layout for smaller parts. This new technology is also suitable for many more applications from all different materials besides the production of air ducts.
ILLIG is a worldwide leading manufacturer of high-performance lines and tools for thermoforming and packaging industry. The business activities include development, design, manufacturing, installation and commissioning of complex production lines and individual components.
With branch offices and representatives ILLIg is present in all markets in more than 80 countries worldwide. The still ownermanaged company has been supporting its customers for more than 60 years now as reliable partner for economic production of sophisticated and high-precision parts from thermoplastic materials. Innovative technology of highest quality and comprehensive, global service are essential elements.