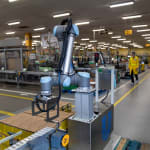
Six cobots by Universal Robots work in the Katowice-based factory of Unilever, one of the world’s largest companies within the Fast-Moving Consumer Goods (FMCG) industry and the owner of around 400 brands, available in over 190 countries. Full automation of palletizing process with cobots increased efficiency of palletizing and moved employees to different tasks. Estimated return on investment in UR collaborative robots in Unilever is around 12 months.
Unilever has four production plants in Poland. One of them, in Katowice, specializes in packing of tea delivered to the factory in 25 kilogram sacks. Cartons with the ready-to-sell product packed by employees to boxes are placed on pallets by six UR10 collaborative robots. The use of cobots shortened the palletizing time, optimized work ergonomics and relieved employees from the most strenuous tasks.
„Deployment of collaborative robots in Unilever plant is a great example of how fast the automation can be implemented and how to speed by this mean production processes and at the same time improve work ergonomics. We are glad that automation specialists from Unilever benefited from Universal Robots Academy and through it gained basic knowledge about implementation, programming and handling of UR cobots. Also, we are satisfied to see that along getting to know the capabilities of our robots, companies identify more and more processes and areas which can be effectively automated. It shows how flexible and universal solution are cobots,” says Slavoj Musilek, General Manager Central and Eastern Europe at Universal Robots.
Cobots as an answer towards current situation on the labor market
The Unilever plant in Katowice employs around 400 people working in two production halls.
“For a long time we faced difficulties in keeping and finding employees for monotonous, manual tasks related to packing and palletizing – tasks that were often strenuous due to product sizes handled. We needed a solution to automate these processes,” says Dariusz Ratajczak, Automation Senior Specialist at Unilever.
However, finding a flexible robot with appropriate payload and reach, as well as intuitive handling and programming was challenging.
Automation of the palletizing process
Unilever fully automated two production lines in Katowice, where six UR10 robots now handle tasks related to packing of the tea. Before implementing automation, all these tasks had been performed by a human. Operators spent around 70% of the time packaging and 30% palletizing. With the palletizing now entirely automated by the cobots, the operators have been freed up from 30% of the tasks. Cobots perform the most tiresome works and are also very efficient – palletizing around 1100 boxes during an eight hours shift. In the process of palletizing, each box is placed on the pallet by the UR10 robot according to a predefined pattern.
Intuitive programming of cobots
At the Katowice-located Unilever factory, the robots’ programming depends on the shape and size of cardboard packaging. However, in all cases this process is similar. After reaching the specified number of boxes on the pallet, the UR10 starts the next layer. The pallet usually contains six to ten layers and has ten to twenty one boxes in each layer. When packaging process on one layer is completed, robot calculates the new height and marks the starting point for the next one. When the operator notices that the UR10 begins to stack cartons on the next pallet, he departs with the already loaded pallet. Completing the pallet takes cobot about 20 to 30 minutes.
Before implementing UR cobots, Unilever automation specialists considered a ready-to-use solution such as palletizing robots. Taking pros and cons into, the team decided that cobots would be more flexible, easier to use and would deliver a quicker return on investment.
“Deployment of UR10 cobots enabled us to reduce the packaging time while improving the work ergonomics considerably. Before automation, employees had to perform monotonous tasks involving bending over to place boxes on lower layers of the pallet. This hardest activity was totally eliminated by UR robots,” says Dariusz Ratajczak.
Future of robotization in Unilever
Implementation of collaborative robots is also being considered at other Unilever plants with automation specialists from Katowice willing to share their experience, explaining how they solved the palletizing problem with cobots. The Katowice team also works on automating the process of depalletizing, enabling the cobots to pick materials for production.
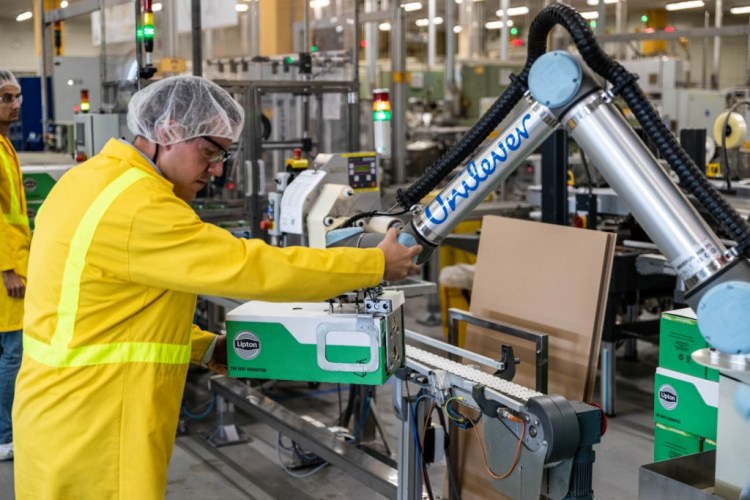