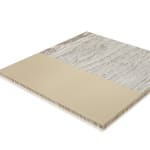
"Experts forecast unparalleled growth rates for LVTs in Europe and North America in the years to come. The growing demand is based on the specific benefits of LVTs in terms of unlimited and appealing design options that range from natural wood to stone optics of any color," reports Hilmar Heithorst, Division Manager for Sheet and Foam Extrusion Lines at KraussMaffei Berstorff. "Thanks to their moisture resistance, they can also be used in wet rooms such as kitchens or bathrooms. In addition, LVTs provide excellent impact sound insulation. They feel naturally warm, but are also suitable for use with underfloor heating. Typical LVTs have a thickness of 2 to 5 mm, are available in commercial sizes of wood-fiber based laminate panels and can be easily connected using the click system," adds Hilmar Heithorst.
LVT flooring is composed of a highly filled core layer - usually provided with an integrated glass mat - plus decorative film and a wear protection layer. While the glass mat gives strength and dimensional stability, the core layer provides flatness of the floor covering and impact sound insulation. For this purpose, the PVC sheet material is filled up to 60 to 70% with mineral additives to obtain thick sheeting of high density and weight. The decorative film is laminated to the thick sheeting to produce the desired design and the product is rounded off by wear protection layers of different thickness depending on the future application.
Similar to roofing sheets, the three-layer floor covering core is produced on two twin-screw extruders and two smoothing calenders. The first extruder - used for plasticizing and homogenizing a PVC compound - is equipped with a side feeder to incorporate a high mineral filler share and additional additives. The material leaving the extruder is applied to the glass mat on the first downstream smoothing calender. The composite obtained is then guided through the second smoothing calender to apply the PVC compound - previously processed on the second extruder - to the other side of the glass mat. This method offers the decisive benefit that processing, compounding and tile production are carried out in-line, which is of fundamental importance for heat-sensitive PVC in particular. Downstream from the second smoothing calender, the three-layer core material is provided with the decorative film and the wear protection layer. The five-layer composite then passes through an embossing station as well as a temperature control section to ensure dimensional stability before being cut to size.