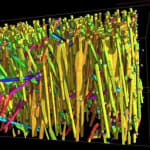
Sigma Plastic Services, presents the latest improvements of its injection simulation software Sigmasoft. A focus of the new developments is the simulation of highly-filled polymers, such as thermoplastics with high percentage of fiber reinforcement.
Following the trend to reduce the weight of molded parts, the demand for highly-filled polymers, such as thermoplastics or thermosets with 50 % or 60 % of fiber content, as well as polymers with metallic reinforcement for powder injection molding applications, has increased in the last years. However, the rheology of these polymers cannot be described with classical viscosity models, such as Cross-WLF or Carreau-WLF. As it was proved by comprehensive trials conducted by Sigma, this modified rheology of highly-filled polymers influences the filling behavior of the melt, as well as the resulting fiber orientation and thus the predicted warpage and mechanical behavior. If the injection molding simulation ignores these factors, the accuracy of the produced results is questionable and only of limited application.
The fiber orientation influences the viscosity and thus the filling pattern. The currently available simulation models cannot reproduce this interdependence. The predicted fiber orientation and the resulting anisotropic mechanical properties are therefore unreliable, particularly in polymers with a high percentage of fiber reinforcement. In Sigmasoft, new models were integrated which reproduce the non-stationary interdependence between the fiber orientation and the viscosity.
In this way, the accuracy of the calculated flow behavior is greatly improved for highly-filled polymers. A further advantage of this expansion lies within the improved accuracy of the prediction of the final fiber orientation, particularly in the middle-layer were fibers are predominantly oriented perpendicular to the flow direction, because the actual interaction between viscosity and orientation is considered.
For the trials conducted at Sigma, 3D-Computer tomographic images, produced by Volume Graphics, were used (Figure 1).
In Figure 2, the fiber orientation perpendicular to the flow direction predicted by the simulation is compared with and without consideration of the interaction between fiber orientation and viscosity. The differences in the prediction of the middle-layer are clearly visible. The influence over the final mechanical properties is evident.