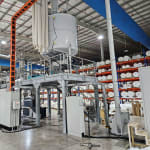
Thanks to new technologies, greater precision in collection and sorting, and the continuous development and refinement of lines and plants, more plastics than ever can now be processed and returned to the recycling and upcycling loop. Recently, a customized, integrated, innovative MAS line went into operation that reprocesses previously disposed of packaging film waste for highly sensitive applications - a major challenge met with ingenuity and expertise.
LLDPE for pet food packaging
The South Vietnamese company Thành Phú Plastic Packaging JSC, a pioneer and innovator in the use of industrial equipment and plastics throughout Southeast Asia, produces a wide range of packaging solutions. Food packaging - particularly pet food packaging -is especially challenging in this specific field. Food packaging must comply with a wide range of laws and regulations and the highest standards, from the quality of the plastic and film to purity and even odor - an important issue when you consider how sensitive pets’ noses are.
One of the key components of pet food packaging is a film made of a special type of LLDPE. The packaging design involves a lot of waste and residual material that is very difficult to recycle due to its light weight and high volume. Accordingly, up to 30% of the raw material used in the packaging film had to be disposed of completely - several tons of plastic per day. For a company that not only strives for technological innovation but also for a sustainable, resource-conserving approach to the environment, this was of course unacceptable.
Holistic MAS line for recycling without pollutants
Contact with MAS was established through the Hamburg-based company Rieckermann, which has had a strong presence in Vietnam for decades. The objective was clear: Plastic waste that had previously been disposed of was to be recycled and fed back into the processing cycle - as gently as possible and with no loss of material, while retaining the high-quality material properties. A specially developed line, tailored to the customer’s requirements and consisting of several MAS systems arranged in series, now processes around 500 kg or 130 m3 of film per hour. This complete system shreds film scraps, melts the material, increases the material quality by adding additives, and filters out both pollutants and unwanted odors. The result: High purity that meets even the strictest standards and regulations.
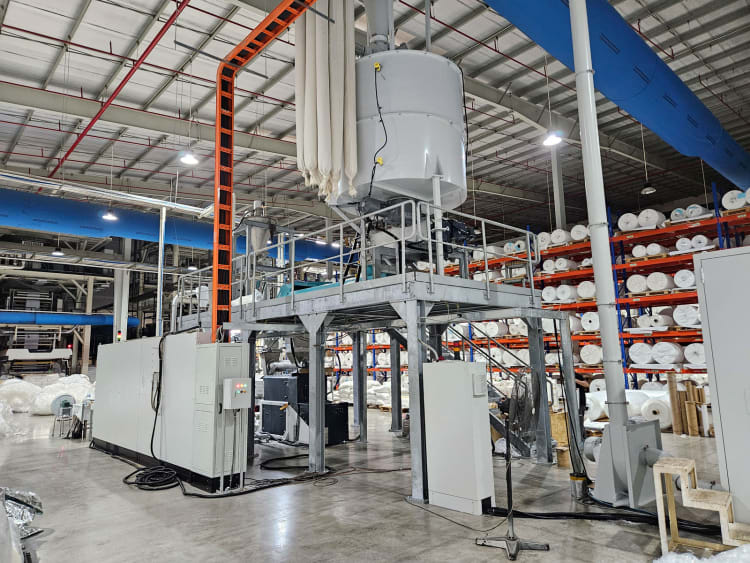
How the customized MAS complete solution works
With the exception of the upstream shredder, the entire line (including the steel structure and platform) was supplied by MAS, carefully delivered to Vietnam, and assembled on site.
- In the shredder provided by the customer, the film scraps and offcuts are shredded into small particles of about 6 mm and conveyed by a blower into a puffer silo which has space for about 200 kg or 6 m3 of film.
- The subsequent belt weigher acts as a dosing system. Weighing cells on the conveyor belt measure the weight and indicate how much material is currently being fed to the extruder. This means the feed rate can be directly controlled and readjusted.
- A stuffer feeds the material into the feeder and finally into the screw, where the large volume of film is compressed and can then be more easily fed to the extruder.
- A connected filter with a fineness of 0.0064 mm separates any contaminants such as stones and foreign particles.
- The material is cleaned again and deodorized via a cascade. The second cleaning stage - the process water vacuum system CC290 - excludes the smallest of other vapors and contaminants to guarantee the best, odorless product quality.
- Finally, the liquid melt enters the granulation unit to produce pellets - the end product for further film production. The pellets are then filled into big bags.
This complete solution was certainly an exciting challenge, and it is also unique in Vietnam. Both MAS and the client Thành Phú Plastic Packaging JSC are proud to highlight their respective pioneering roles with a line that will pay for itself within a few years. Further joint projects are already in the pipeline.
If you are also looking for a customized solution for the recycling and upcycling of various plastic materials to the highest standards, MAS is the right partner for you. We look forward to discussing all your requirements with you and making your plans a reality. We look forward to receiving your inquiry! We are looking forward to your inquiry!