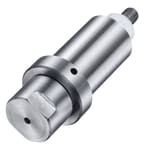
The demoulding stage during the injection moulding process can be optimised through the use of an ejector delay unit. The sprue and moulded part are cleanly separated from one another through a coordinated ejector movement.
The new ejector delay unit Z1725/... from Hasco offers a simple solution for the efficient demoulding and separation of sprues. The unit enables two-stage ejector demoulding, in which the delay is ensured by an individual pocket depth and the ejector assembly.
Through the new delay unit, not only can the process reliability be considerably improved, but also the quality of the end-products. Production downtimes are, thanks to the innovative design of the unit, a thing of the past. In addition, it offers maximum flexibility because they can be used without any minimum stroke requirements. With ejector s from 2 to 5.9 mm, this enables a variety of applications in different production processes.
The functioning of the ejector delay unit is based on the transfer of axial forces through friction between the plastic sleeve and the drill-hole wall. This friction force can be steplessly adjusted by a conical, self-securing screw and adapted to the specific requirements. The plastic sleeve should sit approximately 3 mm deep in the location hole. The precise position of the ejector pin is achieved by a flattened circular pocket, during which the desired delay is integrated into the pocket depth of the ejector package.
Overall, the Hasco ejector delay unit offers an efficient solution to meet challenging demands in the demoulding of injection-moulded parts. The simple retrofitting of existing moulds facilitates its integration into existing production lines.