Recycling on the rise
“New legislation and targets for the recycling of plastics and the use of recyclate are changing the way the whole plastics industry must operate,” says Elizabeth Carroll, Consultant, Recycling and Sustainability, at AMI Consulting in Bristol, UK, which has a new report out on mechanical recycling in Europe. “The mechanical plastics recycling industry, therefore, has become the focal point for investments, acquisition, and expansion,” she says.
Plastics recyclate production in Europe was 8.2 million tonnes in 2021 and is forecast to grow at a rate of 5.6%/year to 2030. That compares with the 35.6 million tonnes of commodity plastics that entered the waste stream in 2021. “This implies that Europe achieved an overall plastic recycling rate of 23.1%,” says Carroll. That figure is most likely to rise as the plastics industry makes major investments in recycling technologies of diverse types.
The picture of how to convert recycled plastics into high-value products is brightening. Says Engel’s Engleder: “Thanks to horizontal networking along the value chain, we will no longer have to downcycle materials in the future, but can actually re- or even upcycle them. If we exchange information and data across companies, we will be able to recycle plastic waste and produce high-quality plastic products from it again. Digital transformation is the prerequisite for rapidly advancing the issues of sustainability.”
At Sumitomo (SHI) Demag, CEO Liebig agrees that recyclate processing in itself is not an insurmountable technological challenge. “The greatest challenge is achieving comparable component performance and stabilising non-uniform material properties through intelligent process monitoring,” he says. “There are many promising projects underway, although recyclate performance is still dependent on purity.”
Michael Ruf, CEO of KraussMaffei, which has injection and extrusion technologies under its belt, says: “Circular Economy is not only an ecological but also an economic imperative. It is therefore a supporting pillar of KraussMaffei's product strategy. Customers have already recycled more than one million tons of plastics with our systems.”
And at compounding equipment company Coperion, Marina Matta, Team Leader Process Technology Engineering Plastics, says: “We are observing many ground-breaking developments that significantly improve the sorting and washing quality of waste. The pyrolysis process has also recently been significantly enhanced so that this recycling process can be carried out in a much more energy-efficient way.”
Polymer suppliers going green
European polymer producers are making major efforts to improve the sustainability of their products. At polyolefins and compounds major LyondellBasell, Richard Roudeix, Senior Vice President - Olefins & Polyolefins Europe, Middle East, Africa and India, says: “Becoming climate neutral by 2050 requires the industry to go through a deep transformation in a relatively short time frame, especially considering that some technologies to completely decarbonise our processes are still in early phases of development. Currently, high costs for energy are compressing industry profits at the exact moment the industry needs additional funds to make decarbonization investments.”
Polymer suppliers have not been entirely eye to eye with European policy makers on how to move to a green economy, but opinions are converging. “LyondellBasell believes alternative government policies and voluntary measures are more effective than relying uniquely on national taxes in achieving environmental goals,” says Roudeix. He suggests that a fee based on a product’s recyclability could be used to fund improvements in plastics recycling infrastructure and programs.
LyondellBasell aims to produce and market two million metric tonnes of recycled and renewable-based polymers annually by 2030. It has already launched plastics made from mechanically and chemically recycled plastic waste, as well as bio-based feedstocks.
Similar comments come from SABIC. In 2019, it launched certified circular polymers produced by upcycling used plastics. “However, the reality is that there is currently greater demand for recycled plastics than the supply available,” says a representative. “Manufacturers need to find a way to scale up in order to instigate real change.”
Greater regulatory support from governments is required to help industry players scale new techniques such as chemical recycling, says SABIC. “For example, it is important that the European regulatory framework recognize chemical recycled resin as equivalent to virgin resin produced from fossil feedstock in order to increase availability and drive scalability.”
At BASF, which like SABIC has a broad pallet of plastics aimed at multiple markets, a representative says: “We expect that plastics will play a vital role in achieving the EU´s net zero emissions goals by helping to deliver emission savings for key sectors like construction, automotive, or food packaging. We are striving worldwide to achieve net zero CO2 emissions by 2050. In addition, we want to reduce our greenhouse gas emissions worldwide by 25% by 2030 compared with 2018.”
Polycarbonate and polyurethanes major Covestro has one of the boldest strategies among polymer suppliers. Its target is to have net zero emissions for scope 1 and 2 (related to its own production and external energy sources) by 2035.
Plastics Europe Managing Director Virginia Janssens, Managing Director, Plastics Europe, says its members support the 30% EU mandatory target for recycled content in plastics packaging by 2030 and have recently announced 7.2 billion euros of planned investments in chemical recycling by 2030 in Europe.
Throughout and beyond what hopefully will be the temporary crises of COVID and Ukraine, “the world remains firmly focused on circularity, plastic pollution, and environmental leakage,” says Wiesweg at IHS Markit. “The circularity drive will spur innovation in chemical recycling, helping achieve world scale commercial viability which along with mechanical recycling will steadily displace virgin plastic resin.”
K 2022 - the world's most important trade fair for the industry
In 2022, as every three years, K in Düsseldorf will once again be the most important information and business platform for the global plastics and rubber industry. Nowhere is the internationality as high as in Düsseldorf. Exhibitors and visitors from all over the world will come together and take advantage of the opportunities from 19 to 26 October this year not only to demonstrate the industry's capabilities and present innovations, but also to exchange views on the situation of the plastics and rubber industry in the various regions of the world, discuss current trends and jointly set the course for the future.
For more information on K 2022 go to: www.k-online.com
Also see the online magazine of K in Düsseldorf at: K-MAG
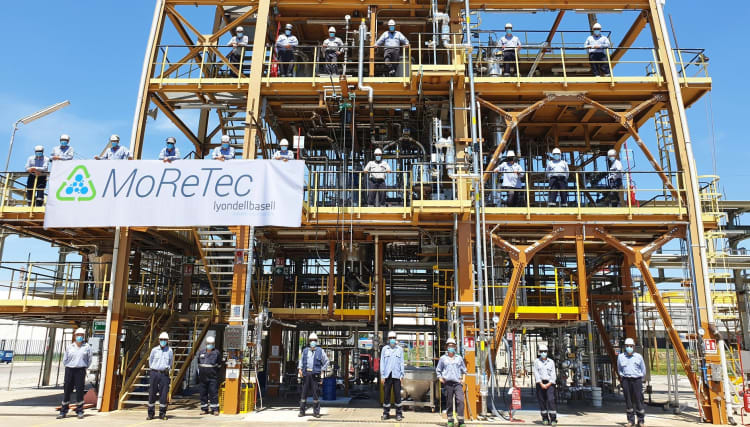
LyondellBasell is developing its own chemical recycling technology, MoReTec, at a pilot plant in Ferrara, Italy. Several other polymer suppliers in Europe are following suit. (Photo, LyondellBasell)