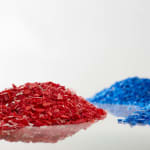
Production of recycled plastic content is far from meeting demand, posing major industry challenges. Embracing the latest technological advancement in flake sorting helps bridge the gap between supply and demand and gives recyclers a competitive edge in efficiency and profitability.
The plastic industry is in transition and facing a set of challenges, the most prominent of which is delivering high-quality secondary feedstock in large enough volumes to meet the ever-growing demand. Over the last decades, plastic production rates shot up unprecedentedly. According to Plastics Europe, global plastic production reached 390.7* million metric tons in 2021, of which 352.3 MT is virgin-based (90.2%) and only 32.5 MT (8.3%) from post-consumer recycled plastics. A closer look at the distribution of the total plastic production by type reveals that polyolefins make up the majority of it with manufacturing rates amounting to approximately 180.5 million MT. Although there is an affluence of plastic on the market and further increase expected, recycling rates remain low and access to high-quality recyclates is limited. In times when legislation and recycled content targets become increasingly stringent and time-sensitive, it is crucial to unlock the potential of existing solutions.
A glance at the current state of recycling shows that waste management infrastructures, from collection to sorting and recycling, have become more mature in numerous countries around the world, but the capacities available are still not keeping pace with the ever-increasing demand for recycled resin. More investment is needed to establish solutions at scale, producing the volumes and qualities required. Fortunately, some bottlenecks can be overcome with sensor-based flake sorting solutions. As part of the recycling process, flake sorting narrows both the quality and quantity gap for polyolefins (PO), polyethylene terephthalate (PET) and a growing number of other applications. Recyclers using the latest flake sorting technology can capture more types of material, maximize yield and maintain profitable operations.
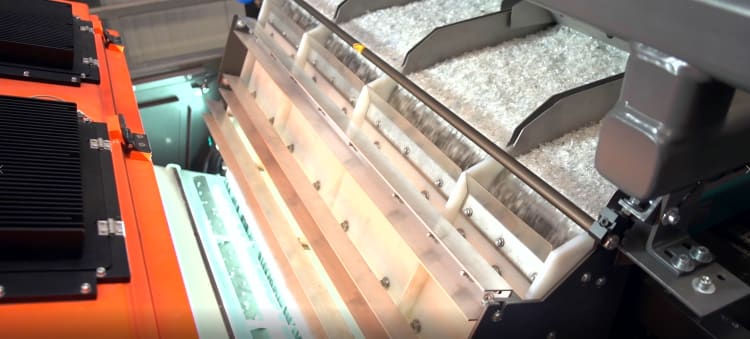
Flake sorter purifying post-consumer plastics
Quantum leap in recyclates quality
Flake sorting is no stranger to plastic recycling. It allows for the creation of high-purity mono fractions of one material type and/or color and is the last purification step before the target fractions go into extrusion. Thus, it is an indispensable component of the recycling process and directly impacts the final quality and yield of the recyclates.
To date, flake sorters are already integrated into numerous bottle recycling plants around the world but hold much more potential. They can also be used for treating mixed plastic waste, unleashing new streams of available feedstock and improving recyclates quality. Often, where no advanced flake sorting solutions are in place, the end product is a mix of different polymer types and, in some cases, numerous colors. Since this fraction contains several distinct product types, its quality levels are low and it can only be used for lower-grade applications, for which demand and value are marginal. The demand for superior secondary feedstock on the other hand is skyrocketing, spurred by stringent recycled content targets as well as the improvement of individual sustainability credentials. With advanced flake sorting, recyclers can easily upgrade their products and create new revenue streams.
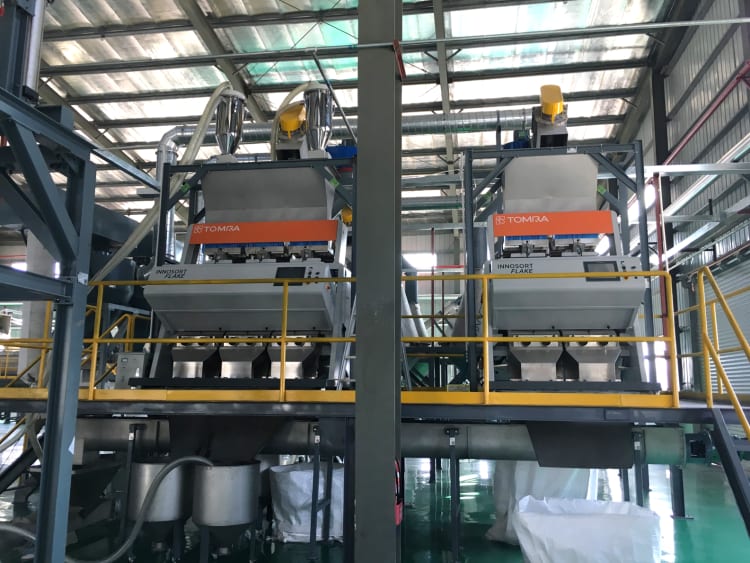
Flake sorters in recycling facility