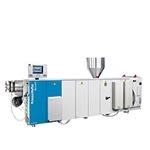
KraussMaffei Berstorff offers an effective response to this problem for its counter-rotating, parallel twin-screw extruders. In machines intended for processing polyolefin- and PVC-based natural fiber composites, the core element, the processing unit, is supplied with extra wear protection.
“Wear protection optimized for the material being processed guarantees far longer service lives for the processing units; this minimizes downtime and the associated maintenance costs and loss of productivity,” says Michael Finkenzeller, Product Manager Renewable Raw Materials in the Extrusion Technology Division at KraussMaffei Technologies GmbH.
Increased expansion forces can occur during processing of resin compounds and result in adhesion wear on the screw outer diameter and in the barrel bores. To reduce this adhesion wear, KraussMaffei Berstorff has adapted the screw geometry to optimize flight and inter-screw clearance. The service life of the processing units is also substantially extended by tungsten-carbide armoring on the screws and bimetallic-plated barrel bores.
When wear does cause problems, processors nonetheless benefit, because they need only replace the bimetallic bushing and not the entire barrel. The cost savings of this approach are substantial. Apart from adhesion wear, abrasion wear can also be a problem in processing natural fiber composites. KraussMaffei Berstorff counters this problem by giving the screws a protective hard chrome plating.
Counter-rotating twin-screw extruders are used worldwide for processing plastics reinforced with natural fibers, for example, wood plastic composites (WPC). This type of KraussMaffei Berstorff extruder also features a number of other benefits, for example, steady material feed, gentle, non-destructive processing and highly stable screw pressure for the production of intermediates.
In addition, they are an optimal solution for processing ready-to-use compounds. High installed screw torque combined with a long processing unit guarantees very high output rates. The special screw geometry is gentle on the material and delivers a homogenous melt at an optimal temperature, even with high melt pressures.
Because of their longer life, natural fiber composites are replacing pure natural materials, such as wood, in many areas. Typical examples are decking, fencing and screening. KraussMaffei Berstorff offers complete, application-specific system solutions for all these types of product.