PX 121-180 SilcoSet: Live production of matrix lenses made of LSR
Silicones, and particularly the new generations of LSR (liquid silicone rubber), continue to conquer new application areas thanks to their excellent physical property patterns, offering great opportunity for growth. At the same time, however, they burden the processor with challenges when it comes to precision and process consistency in the injection molding process. At the NPE show, a PX 121-180 SilcoSet produces matrix lenses for the headlight industry.
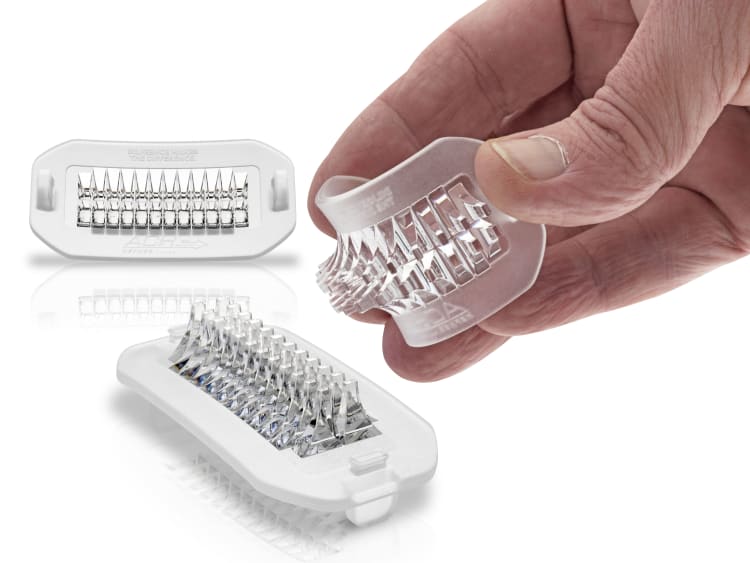
The machine function APCplus supports a sustainable production here by continuously analyzing the injection molding process and quickly and accurately compensating for material- and environment-related fluctuations in melt viscosity. This ensures a consistently high component quality and thus minimum scrap.
The two cavity LSR matrix mold comes from mold specialist ACH Solution providing best temperature balancing even with longer scheduled downtimes. The ACH Servoshot 2G stands for precise needle valve regulation. The linear robot LRX 150 from KraussMaffei with EOT from ACH Solution allows an inline production with inspections, weight check and separation.
Large-scale production also in aviation - Partnership with NIAR
Another highlight at the KraussMaffei booth is the manufacturing demonstrator Frankenstein from the National Institute for Aviation Research (NIAR) at Wichita State University. It showcases different examples how to introduce automotive-matured ultra-high-rate manufacturing technologies to aerospace – a joint research program NIAR and KraussMaffei are driving forward with together.
In addition, NIAR will show the inlet duct of a 10-meter-long unmanned system manufactured using a proprietary meltable tooling concept developed by Fiber Dynamics, Wichita, Kansas/USA. A further highlight is an aircraft window plug that is currently undergoing certification efforts for aircraft passenger-to-cargo conversion activities at NIAR.
These composites parts are manufactured using the FiberForm technology developed by KraussMaffei. The process combines the thermoforming of organic sheets and injection molding in a single process. The result is particularly lightweight fiber-reinforced plastic components with a high level of strength. Until now, they have mainly been used in the automotive industry. The cooperation between NIAR and KraussMaffei has now paved the way for FiberForm to be used in aerospace applications as well.
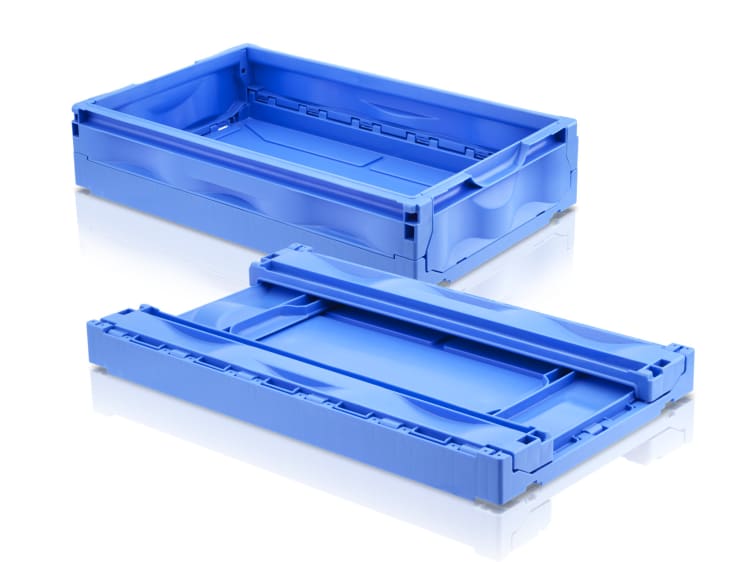
Future mobility - Clemson University shows driverless concept vehicle
Another partner at the KraussMaffei booth will be Clemson University. They will showcase its advanced materials and manufacturing expertise via multiple projects in mobility industries. Specially highlighted is an ultra-efficient driverless concept vehicle designed for the year 2035.
Clemson students and faculty worked with ExxonMobil Chemical and Honda North America to engineer, build, and validate the prototype with a special focus on sustainability, resulting in a design with 18% plastics and composites by weight – nearly double the 10% market average. Built with reclaimed, lightweight, and recyclable advanced materials, the project exemplifies the highly translational and rapid R&D engineering possible at Clemson.
Ultra lightweight: Premiere for first HP-RTM bike in the US
TIME Bicycles, in partnership with KraussMaffei, Fraunhofer USA and Clemson University is raising the bar of composite bicycle technology through a special development project to introduce HP-RTM (High Pressure Resin Transfer Molding) to the cycling industry.
At the NPE show, they are showcasing the first, USA produced HP-RTM bicycle to the world. Visitors to the show have the possibility to register for a giveaway from the first production. Retail value of the complete bicycle is 8,000 USD. TIME Bicycles was founded in France in 1987 and is the leading European manufacturer of carbon fiber bicycles, specializing in Resin Transfer Molding (RTM).
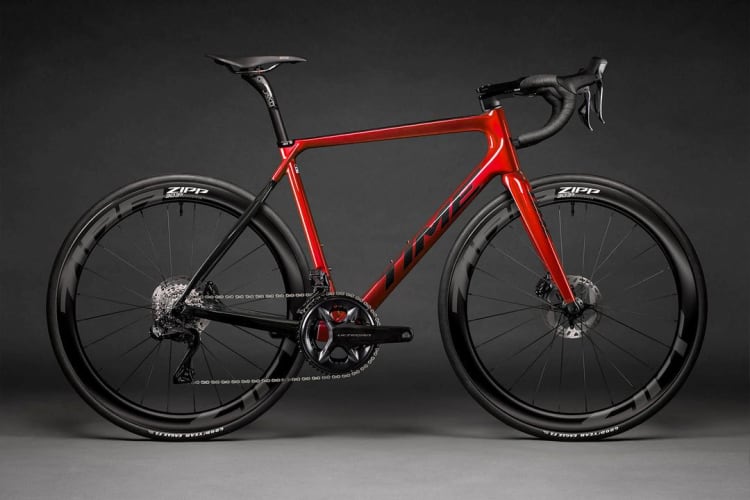