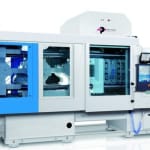
An all-electric EX 80-380 SilcoSet containing CleanForm cleanroom modules for a clean mold area will produce teats made of liquid silicone rubber (LSR).
The all-electric EX is predestined for the production of complex moldings and offers maximum dynamics and precision. The very low viscosity of the LSR requires a processing system with minimal venting gaps and special seals in the sprue zone. To prevent flash, the injection molding machine must maintain high platen parallelism. The EX Series scores here with precise platen control guaranteeing exact parallelism at all times.
"The metering precision of the all-electric plasticizing unit ensures that the mold cavities are filled exactly with no risk of over-feeding", said Bruno Schleiss, Managing Director of Krauss-Maffei (Schweiz) AG. "The outcome is improved product quality and minimized mold wear." The optimized length of the compact LSR plasticizing unit ensures an extremely compact machine solution.
Uncompromisingly geared towards cleanliness, efficiency and precision, the machines can be used up to cleanroom class A according to GMP. "We offer customers excellent value-added through our CleanForm GMP solution.
Production costs can therefore be reduced by up to 25 per cent by, for example, transferring the produced parts to sterile packaging directly after demolding. This means that subsequent sterilization is no longer required", explained Schleiss. A closed oil lubrication system supplies the pivot points of the Z toggle and prevents lubricants from leaking. Fewer pivot points, all completely encapsulated, and tiebars that no longer act as guides for the moving platen eliminate potential sources of impurity. The production cell therefore operates virtually without particles or thermal emissions.
The impressive features of the machine are its efficiency, fast speed and uncompromising design in regard to cleanliness. It is therefore ideally suited to precise and cost-effective production in the medical and packaging industries.
The unique Z toggle ensures fast mold movements of the clamping side while direct operating principles of the plasticizing and injection unit lead to maximum process accuracy. Since every axis of the EX has its own electric drive unit, both the injection unit and the ejector can be operated in parallel. Once again this reduces the cycle times. Since the EX machines can be equipped with numerous injection units, they are suitable for the production of small precision parts and for production in the highperformance segment with high shot weight and material throughput with a short cycle time.
For 10 years KraussMaffei has had a clear profile in Switzerland as a complete supplier of Injection Molding Machinery. Modern machine technology in the entire clamping force range from 35 to 4,000 tones, the large number of linear and industrial robots, and the cross-process production solutions from a single source form the basis on which our experts produce the suitable production cell for every customer. From standard solutions based on pre-configured production cells, for example the CX ClassiX, through to complete production cells for complex automation tasks for customers in many different sectors of industry.