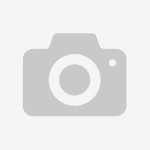
These include: in the transport sector, KK - KruiseKontrol, an exclusive system for conveying plastics granulate at constant speed; in the drying sector, the evolution of the Dry Air mini dryer; in the blending sector, the latest DGM gravimet-ric blender.
These innovations are part of a larger project that brings touch screens to various product lines, including X Dryer, Dry Air, KK – KruiseKontrol, Gravix, Quad, Flowmatik, MPK, Dolphin, and BCS – Bar Code System. In this way, the interface between the operator and the machine is further improved with a simple, clear and intuitive system.
The KK - KruiseKontrol provides an innovative way of controlling the granule transportation to the processing machine, avoiding problems that could compro-mise the characteristics of the finished product.
Vacuum transport is not as simple as it may seem. Different types of granule be-have in completely different ways, depending on their bulk density, fragility, powder content, granule shape, additive content, how far the granules have to travel and so on. All these differences have been taken into account in the development of KruiseKontrol, so that it can optimize transport parameters.
The user indicates the type of material to be transported and the number of the machine to be fed, and KruiseKontrol creates the most suitable set of transport parameters. It is capable of controlling the velocity best suited to each material, without damaging it and avoiding the formation of powder along the pipeline. There are none of the normal initial and final peaks in the velocity profile, while velocity during the middle transport phase is increased, yielding an overall in-crease in productivity (see graphic). The system also avoids the damaging of the granules running in the pipes.
Transport velocity can be different for every cycle, but the set velocity is maintained whatever the conditions, the length and the height of the pipeline. The result is the total elimination of powder formation, less wear on the pipes and the complete elimination of the “angel hair” phenomenon – the formation of what looks like long strands on the inside of the pipe. Only one vacuum generator is needed for several zones of the system.
The new system has no rival for processing engineering plastics, in particular for optical disc production. What is more, it is extremely simple to use. The control system has a dynamic structure: parameters are set as default value and it is sufficient to match the material to the machines to obtain a dedicated conveying system with constant velocity. Touch-screen control makes this operation very simple.
Evolution of the Dry Air mini dryer and developments in the X Technology range Dehumidification is Moretto’s core business. It has developed several technologies, but the Dry Air mini dryer has been particularly successful. The Dry Air is a dehumidifying dryer with twin self-regenerating towers, for small operations, suitable for the production of small technical products such as small camera lenses, phone components and the like. It makes use of zeolite (molecular sieve) technology. It uses compressed air directly from the factory network, without pre-drying. Its “anti-stress” function monitors the temperature of the return air, reducing the flow of delivery air when this temperature gets too high, in order to protect the material from thermal stress. The Dry Air project includes five mod-els, each with its own hopper. Machines are very compact and, thanks to their reduced dimensions, can be installed directly on the injection moulding machine.