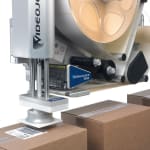
Products that are bundled, boxed and ready to begin their journey along the retail supply chain require an identifier. A box of product without this will not get very far, and will certainly not reach its intended destination with any form of ease, therefore a label detailing its contents is necessary. In order to achieve this, LPA systems print and apply labels to outer cases as they roll off the production line.
Today, consumer demand for choice has led to many variations of products being required. As an example, you may have a chocolate bar that is available in plain, milk, raspberry and mint flavours - each requiring its own unique identifier. This has fuelled the need for nimble, flexible LPA systems that can be adapted quickly and efficiently where many fast changeovers are required.
The regulatory landscape, too, has been an important driver in improved technologies around LPA. Food safety concerns are a high priority across the board and regulations require products to be labelled with accurate, readable codes. This enables particular batches to be isolated should a fast product recall be required, and could significantly reduce the negative impact of that recall if the company in question can demonstrate the ability to identify and remove unsafe product straight away.
The obvious choice
There are two main ways to print labels onto outer cases. One is via a process called flexography, which is the printing of the entire outer case before it is filled. While this is a reliable process, there are obvious drawbacks in modern manufacturing operations in that it requires that manufacturers hold enormous quantities of stock for each SKU produced. Every time a product changeover is effected, the packaging will also need to be changed at the same time, making the process more time consuming. This downtime leads to loss of operational time, which will inevitably affect profitability.With an LPA system there is no such issue, as the label itself can be changed with very little input from operators. Intuitive systems enable new information to be added with little or no chance of error, meaning a changeover can be carried out on-the-line. This in turn negates the need to carry an inventory of packaging for the various SKUs and the associated storage and downtime expenses.
Addressing common challenges
Misapplied labels, label jams, wrinkled labels and the need for constant mechanical adjustment of labelling equipment are common issues manufacturers face.In order to maintain maximum uptime, which can be detrimentally affected by these issues, systems such as the 9550 Print & Apply Labeler have been developed to alleviate those issues with minimal operator involvement. For example, Intelligent Motion direct drive can enable label speed and position to be controlled without clutches, rollers or adjustments, and a simplified web path means label changes can take place in less than 60 seconds.
Tension can also be automatically adjusted via an electronic supply reel, which maintains the correct tension irrespective of speed and label size from the start to the end of each reel. Printhead pressure is automatically regulated to ensure optimum quality and maximum printhead life, while labels are applied using a simple, single roller wipe action to wrap case corners, removing unnecessary complexity and time from the process.
The interfaces utilized by operators are also highly intuitive and simple to operate, which not only gives peace of mind where errors are concerned, but also enables those operatives to focus on other duties on the line. Code Assurance software can be built in to eliminate operator error and ensure products are coded correctly, while a database minimizes operator touches to ensure accurate job selection.
Interface allows for quick diagnostics and job selection, meaning changeovers can be made simply and quickly while any errors can almost always be identified before they lead to a situation that causes unscheduled downtime.
Corner Wrap: the evolution of technology
Visibility of labels is of paramount importance and in addition to straightforward label application, technology has now been developed to allow a label to effectively be placed 'around a corner'. This technology is ideal for cases or shrink wrapped products where the label must be applied across adjacent panels, so that label info can be seen in various orientations. In many instances, a manufacturer's distribution and retail partners require this.This is typically accomplished by applying labels with duplicate information on both a side and end panel. While this can be done by applying two separate labels, this approach is inefficient in terms of capital budget allocation (i.e. two labelers) and ensuring the label information is synched. The preferable approach is a single unit that can print the information on one continuous label and, in a single process, apply it to adjacent panels on the case. This arrangement is perfect for production floors with limited floor space.
Uptime is critical
Uptime is highly critical and manufacturers may want to look at three areas of interest when looking to purchase an LPA system.The first is design. A well designed LPA system should eliminate mechanical adjustments, wear parts, and any failure points that cause everyday operational problems, such as label jams. Through automatic and precise mechanical control, it is possible to eliminate downtime issues commonly associated with labeling systems, and the ability to design these features into a labeler comes with many years' experience. For example, plant air is a common cause of misapplied labels, as are tamp applicators. Through direct apply advancements and the removal of plant air from the process, design has helped to improve uptime levels for many manufacturers.
Secondly we must look at technology. Code Assurance, as we have mentioned, reduces operator error with intuitive touchscreen interface, while Intelligent Motion technology reduces the top five causes of downtime (label, web, ribbon jams, mechanical failures & adjustments), improving end-of-line efficiencies. By also eliminating more than 80% of wear parts, there is no need for constant ongoing maintenance.
Finally, there is usability. The focus of any manufacturing operation should be on production, not the printers tasked with applying labels to outer cases. As such, it is important to know that the systems installed to undertake a specific job will do so without issue and with the minimum amount of interaction by human hands. The aforementioned advances in technology will allow this to become a reality, ensuring that what is delivered from a labeling system are three of the most important manufacturing must-haves - accuracy, reliability and efficiency.