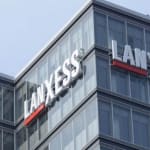
At this year's Fakuma, Lanxess is focusing on new materials for structural lightweight construction, LED lighting technology, electrical and electronic applications and exterior body panel applications. The company will underline its credentials as a strong partner for the plastics industry that both supplies its customers with innovative materials and provides reliable support throughout the entire development chain of the component – from the concept phase and computational design to mold construction, testing and start of series production.
Ready for large-scale series production – multi-axially reinforced Tepex
One hot topic for the future are the new, multi-axially reinforced versions of the Tepex dynalite thermoplastic high-performance composites. In these semi-finished composites, also known as composite sheets, the individual layers of continuous fiber can be arranged not only in the direction of production or perpendicular to it, as was previously possible, but at nearly any desired angle. As Martin Klocke from Technical Marketing and Business Development for Tepex automotive applications in the High Performance Materials (HPM) business unit of Lanxess explains, "this means laminates can be built up with multi-axial reinforcement to precisely meet the specific load requirements of the component. Fully exploiting the potential of fiber direction results in thinner – and therefore lighter – designs at comparable strength."
Thermally conductive – new polyamides for LEDs
For LED lighting technology, Lanxess will be showcasing new reinforced polyamide 6 compounds from the Durethan brand at Fakuma. These compounds conduct heat efficiently while at the same time being electrically insulating. Their thermal conductivity lies between 0.8 and 3 W/mK. Possible applications include cooling elements that dissipate the heat generated by LEDs, thus preventing any decline in brightness or lifespan. Highly reinforced, white, light-reflecting and halogen-free flame-retardant material grades are also in development, for example. "Our calculation expertise enables us to construct LED components in a perfect plastic design in terms of heat dissipation," says Thomas Malek, New Business Development Manager LED at HPM.
Circuit breakers – one material for several performance classes
Among the innovative materials for the electrical/electronics (E/E) industry are reinforced, but nonetheless very low-distortion polyamide and PBT compounds and extremely easy-flowing PBT variants for the cost-effective production of thin-walled components. Holger Mersmann, head of E/E sales at HPM, says: "One special feature, for example, is a glass-reinforced, halogen-free flame-resistant polyamide 6. With its high thermal stability and mechanical strength, it represents an alternative to corresponding mineral-filled polyamide 6 grades. Since it can be used in different performance classes, our customers now only need one material instead of several, which reduces complexity and ultimately cuts costs."
Wide range of potential body panel applications
Lanxess has built up a wide variety of polyamides and polyesters for car and truck exterior body panel parts under the Durethan (PA 6, PA 66) and Pocan (PBT) brands. This includes high-modulus grades for very stiff components, online-paintable PBT grades, low-warpage materials for high-precision applications (seamless look) and customized materials for parts that are at risk of high impact, such as front grills. “Our products offer greater design flexibility than thermosetting systems such as sheet molding compounds, are lighter than metals and result in components with an outstanding surface and excellent paintability that do not require reworking,” explains Sarah Sangermann, project manager for Exterior Body Panels at HPM. Highlights include the glass-sphere-filled PBT Pocan B 5220 XF for online-paintable, dimensionally stable fuel flaps and the non-reinforced PC+PET blend Pocan C 1206 for thin-walled front grills with class A high-gloss finish.