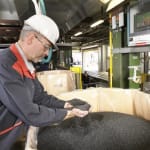
In the plant, the basic polymers polyamide (PA) and polybutylene terephthalate (PBT) are mixed and refined with special additives and glass fiber, according to client requirements, to make the high-performance plastic product lines Durethan and Pocan. They are used primarily in the automotive industry to manufacture lighter-weight plastic components that can replace metal parts in vehicles, contributing to greater fuel efficiency and reduced emissions.
"This investment shows our strengthened focus on high-performance compounds and underlines our strategy to shift this business towards higher-value-added markets," said Hubert Fink, Member of the Board of Management of Lanxess AG. "The capacity expansion in Gastonia also shows our commitment to North America, which we see as major growth region."
In the coming years, Lanxess plans to further invest EUR 50 to 100 million for organic growth in its high-performance plastics business. "With the investments, we will be further balancing the capacities in our polyamide value chain and driving the globalization of our engineering plastics business," said Michael Zobel, head of Lanxess' business unit High Performance Materials.
Lightweight automotive construction as key driver for high-performance plastics
Lanxess expects global demand for engineering plastics in automotive applications to grow by 7 percent annually (CAGR 2015-2020). This is being driven by rising car production and the trend towards more fuel-efficient automobiles. E.g., in the U.S., automakers must meet government-mandated Corporate Average Fuel Economy (CAFE) regulations which indicate the average distance that has to be covered per one gallon of fuel. By 2025, an average fleet-wide fuel efficiency of 54.5 miles per gallon will be required compared to 34.1 miles per gallon in 2016."The U.S. automotive sector remains strong, and the demand for engineering plastics in cars is growing," said Antonis Papadourakis, Lanxess Corporation President and CEO. "With our expanded capacity, we are in a position to support this growth and remain a reliable supplier to our North American customers."
Lanxess is a global leader in plastic-metal hybrid and composites technologies that enable engineers to cost-efficiently reduce part weight in automobiles. Depending on the component, a part designed with high-performance plastics can weigh 10 to 50 percent less than a metal version. Lanxess plastics are used, for example, in engine applications, door structures, front ends, pedals, and interior components. Another field of application is the electrical and electronics industry.
Lanxess' global production network for high-performance plastics
The business unit High Performance Materials is highly backward integrated in the value chain. It produces the precursors for its high-performance plastics, like glass fibers for the PA and PBT compounds and the polyamide 6 monomer caprolactam, all in its own plants.The business unit, with roughly 1,500 employees worldwide, operates production facilities in Belgium (Antwerp), Germany (Krefeld-Uerdingen, Hamm-Uentrop, Brilon), China (Wuxi), India (Jhagadia), United States (Gastonia) and Brazil (Porto Feliz). It is part of the Performance Polymers segment, which generated around EUR 4.1 billion in total sales in fiscal year 2014.
Lanxess is a leading specialty chemicals company with sales of EUR 8.0 billion in 2014 and about 16,300 employees in 29 countries. The company is currently represented at 52 production sites worldwide. The core business of Lanxess is the development, manufacturing and marketing of plastics, rubber, intermediates and specialty chemicals. Lanxess is a member of the leading sustainability indices Dow Jones Sustainability Index (DJSI World) and FTSE4Good.