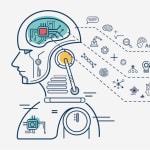
Not long ago, artificial intelligence was still just a playground for software giants. But now it’s arrived in the development departments of machine builders and logistics firms.
Artificial intelligence (AI) is already omnipresent for some tasks in the packaging industry and in logistics. Even though the technology is still in its infancy, you can already begin to see how it will raise automation to a whole new level. According to a survey by the Deloitte consulting firm, the shortage of AI capabilities that is often projected for Germany will only slow down this development, but by no means stop it. Many companies are collaborating with technology giants like Google and Microsoft. Others are relying on their own development skills to integrate learning-capable systems into their processes.
Applying artificial intelligence is an obvious step if only because so much data is already being collected today. Whether the information comes from sensors, warehousing or marketing – every segment of a company is a source of valuable information that needs to be mined. So the data are already there. But putting them to worthwhile use calls for intelligent systems, and increasingly, artificial intelligence as well. With the right algorithms, machines can detect patterns in data and make decisions autonomously. And when the packaging machinery industry talks about artificial intelligence, what's usually meant is machine learning.
Robots go to school: Learning by repetition
Machine learning is really just a subsegment of artificial intelligence, though the two are often used synonymously. It’s actually about optimising production processes in such a way that, for example, they can be performed automatically by packaging robots. But to do that, image recognition systems are an indispensable prerequisite. For instance, if pick-and-place tasks are to be automated, the robots are fed camera information online about the position, location or quality of the product to be packaged. Then they can grip it reliably, or ignore it if it’s defective. This task is often already fully automated today, and is used to pre-group packaging components like lids and containers, or to place foodstuffs reliably in trays.
But increasing numbers of consumer product makers also have to put out ever-smaller batch sizes on their packaging machines, in frequently changing product ranges. The resulting need to change the machines’ format and reprogram the controls causes production downtime. Smart robots can significantly cut retooling time, so product groups can be packaged considerably faster.
The robots detect patterns and compare behaviour, which can let them quickly recognise new products automatically and adjust the packaging process accordingly. That ability is based on concepts like deep learning, founded on neural networks that can be trained from patterns or pictures. The principle of pattern recognition can be applied with equal efficacy to predicting machine failures or wear as well.
When robots plan: Predictive maintenance and optimized processes
Predictive maintenance uses sensor and machine data to permit conclusions about performance or impending events. Machine learning enables the equipment to distinguish between normal conditions and deviations. Gathering so much information makes it possible to detect problems in a machine early, and to remedy them on a planned basis before malfunctions shut down production. In other words, such events become learnable and detectable. As a result, machine makers can schedule service visits, further optimize machine availability, and thus offer their customers greater productivity.
Artificial intelligence in logistics
Aside from predictive maintenance, industrial image processing and controls for packaging robots, artificial intelligence is also increasingly coming to be used for internal and external logistics. Automated guided vehicles (AGVs) are performing more and more tasks similarly to robots: they get their commands directly from a higher-level IT system – for example, when materials need to be retrieved from the warehouse to the production line – and then perform their tasks entirely autonomously.
In higher-level logistics processes, predictive analysis provides a basis for precise predictions about changes that can be expected in material flows. For instance, according to the BVL, Germany’s logistics industry association, AI-based methods are now being used to analyse risk from suppliers, to project foreign exchange fluctuations in international procurement, and to foresee potential supply difficulties together with their impact on production. The Fraunhofer Center for Applied Research on Supply Chain Services (SCS) has taken up artificial intelligence as a topic, and will be reporting on its current findings as part of the TechBox at FachPack 2019. On 26 September 2019 the presenters will be discussing topics like how dispatchers can use data-based prediction and optimisation solutions to apply resources more efficiently, and thus both save on costs and increase customer satisfaction.
Source: Fachpack