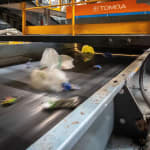
Today’s optical sorters are finely tuned machines. Their software and hardware components work together in a carefully orchestrated symphony to deliver high purity recycled product from complex feedstock at high throughput rates. Sadly, if even one of the components is out of tune, the entire circuit’s productivity and final product purity suffers.
Selecting the right piece of equipment with the right technology supplier is just the first step in delivering the desired performance. Every day, week and month, the machine’s conductor, also known as the operator, must keep a careful eye on and maintain the components to ensure it works at peak performance to optimize profitability.
To do so, consider following these tips for properly maintaining the sorting equipment.
Eye can see
Optical sorters found in the typical MRF or MSW sorting plant process what the human eye can see but at much higher rates. While optional technologies are available to meet specific application needs, two standard technologies are often employed by most sorters:- Visual spectroscopy (VIS)
- Near infrared (NIR)
To see the material correctly, it is crucial that the sorter’s illumination unit is calibrated, so the software detects color and material properties properly. Any environmental change - bulb wear/aging, temperature variations, etc. - can alter the way the sorter sees material.
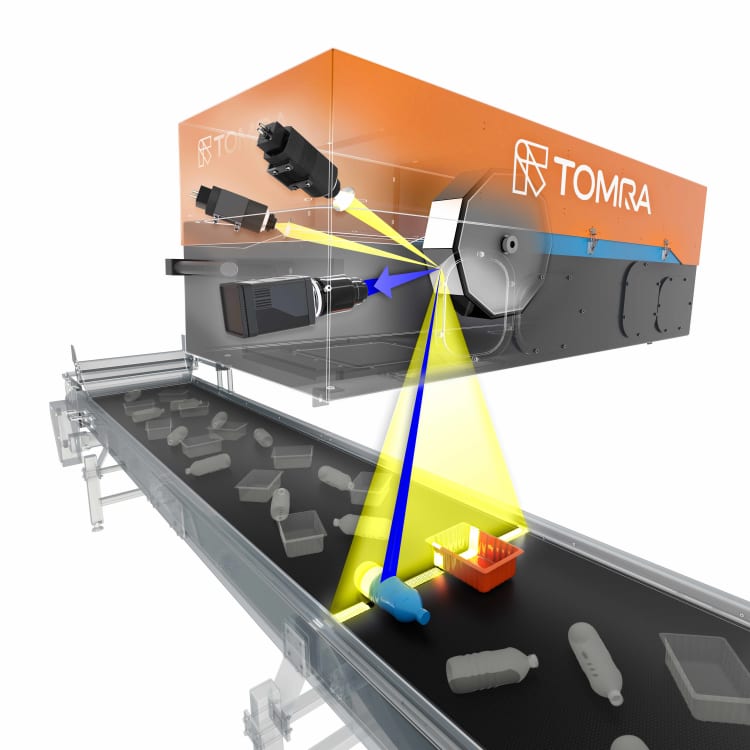
Autosort’s illumination unit for accurate material detection
Calibrating the sorter on sometimes a daily or weekly basis helps to optimize sorting performance but can cut into the production schedule.
When working with your technology supplier, ask how quickly and how often calibration should be performed. Some optical sorters, like the Tomra Autosort, offer continuous sensor calibration, which constantly computes and maintains the VIS and NIR signals to tolerance.
Valve check
All sorters use the same mechanical process to sort material. Air valves produce jet pulses of air at precisely timed intervals to eject either the desired material or impurities in a touchless sorting process. The valve blocks on these sorters can have hundreds of individual valves, depending on belt width.To work properly, these valves must remain clean and clear of debris. Just the operating environment or oil/water in the air lines can clog or completely block a valve, leading to recycled product purity suffering.
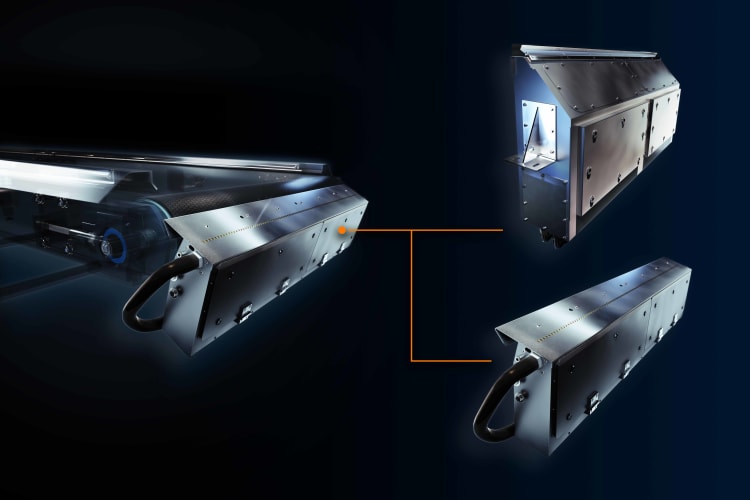
Valve blocks
Workers must perform a valve check for high and low pressure to make sure each valve is working properly. This is a critical maintenance step, since a broken or clogged valve leads to lost output or contaminated final product.
In the past, this required the technician to go to each machine separately to manually perform the valve check. This frequently led to human error when assessing and documenting valve performance.
Today, some, but not all optical sorters offer auto testing and cleaning of the valves to ensure optimal sorting performance and purity. The testing/cleaning process occurs automatically when the circuit stops, removing the chance for human error. Detected damaged valves are reported on the machine’s control panel, or, in the case of a connected machine, to the control room or machine app.