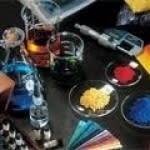
It is estimated that masterbatches will grow over 8% through 2013 in these countries. 2008 saw a growth of 8% despite an economic slowdown, supported by robust growth in the automotive and electrical sector. Demand is stronger for large commodity masterbatches in China where coloring with masterbatch is quite prevalent. Growth of packaging sector has helped in growth of masterbatches.
China accounted for over half of the near 800,000 ton consumption of masterbatch in the region in 2008. All of the leading global producers have plants in China including Cabot, Clariant, Dainichiseika, DIC, PolyOne, Schulman and Toyo Ink. The leading Chinese-owned companies include Melian Chemical and Ngai Hing Hong. South Korea, the second largest market in Asia, accounted for around 13% of demand in 2010.
It has a well developed market as local processing is relatively sophisticated and operates at Western and Japanese standards. Leading suppliers include Cho Yang, Clariant and Toyo. Taiwan, another leading market, has seen slower growth as plastics processing has been relocating to the Chinese Mainland and elsewhere in Asia, where Taiwanese masterbatch companies have been expanding production.
One of the leading producers is Cheng Feng Enterprises, which has plants in China and Vietnam as well as several sites in Taiwan as it has been difficult for foreign companies to penetrate the market which developed at an early stage with locally-owned firms. Taiwan market has relatively lower foreign investment. The largest and most significant foreign investment is that of Clariant. In addition to Cheng Feng, other leading suppliers include Nan Tsan Industry and Ta Chung. The largest masterbatch producer in Thailand is Ampacet, producing white and additive masterbatch. Ampacet has substantially increased its capacity in recent years to add colour and additive products. It primarily makes colour masterbatch for the local market and white and additive more for export markets.
The performance of the masterbatch market in Thailand in 2008 was one of the weakest in the region. The most rapid growth has been seen in Vietnam where there have been very strong increases in plastics processing over the past five years, although the use of masterbatch products is relatively unsophisticated with the market similar to that of China 20 years ago.
Asia is the fastest growing and most dynamic market for thermoplastic masterbatch products in the world. Despite the impact of the global recession demand for masterbatch products has continued to power ahead in the region and is forecast to continue growing by over 7% pa, as per another report by AMI Consulting. The most significant driver of this demand is the continuing expansion and rapid development of the market in China. China is the dominant force in the Asian masterbatch industry accounting for around 60% of demand and production.
In China, masterbatch production has grown rapidly over the past five years more than doubling to meet a comparable increase in demand. Over the same time, China has moved from being a net importer to a net exporter of masterbatch which is starting to have a profound influence on its Asian neighbours with increasing volumes being exported (often at very competitive prices). China is now a net exporter of all main masterbatch types with the exception of additive varieties where the investment in production has lagged the 30% pa growth there has been for additive masterbatch in China over the past five years.
Additive masterbatch demand is expected to be a strong growth driver for the Chinese masterbatch industry going forward as processors and end users demand greater functionality and performance from products. For reasons of cost and tradition, many Chinese processors continue to use dry blends and pigments instead of masterbatch, especially when the resulting product is destined for the local market and not for export.