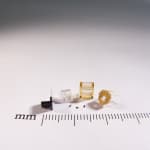
As manufacturers begin to consider the development of parts and components that will need to be micro molded, it is important to bear in mind some key issues from project inception. The start of any micro molding project should begin with all stages required in product development considered from the earliest preliminary design. You need to understand the basic design approach and really bottom out what you can and cannot do, as when micro molding, even the smallest design change can be catastrophic and completely derail a project.
Design for Manufacturability (DfM) is a fundamental consideration when micro molding. In fact micro molders suggest that there should be a subset of DfM, basically DfMM (design for micro manufacturability), as the rules of the game are so different when designing miniature parts or parts with very precise elements and tight tolerances.
Design engineers can create the most incredible parts, but they can be impossible to make. Any design at the micro scale requires careful attention to what might otherwise not be a big deal for larger parts. Each micro molding project is unique in terms of geometric complexity, shape, and can be made in a wide range of materials, all of which will ultimately affect the ability to manufacture.
In this article we will focus heavily on issues concerning material choice, again a vital and early consideration when initiating a product design. A material change can have a profound effect on a part that has exacting levels of detail. Any design engineer will be used to considering stack tolerances and stack dimensions, but when parts get smaller and smaller, the amount of change becomes more of a limiting factor.
If a material is used in a macro molding application its behavior is likely to vary wildly from its use in a micro molding application. This plays to the fact that success when micro molding requires a close and collaborative relationship with a company expert in the vagaries of the micro molding process, and aware of the critical need to select the right material early in the design phase of product development.
Ultimately, material choice has a direct influence on end-use part functionality and it affects tolerance attainment, the achievement of dimensional objectives, and strength parameters. It also has a direct and obvious impact on the cost and timeliness of manufacturing.
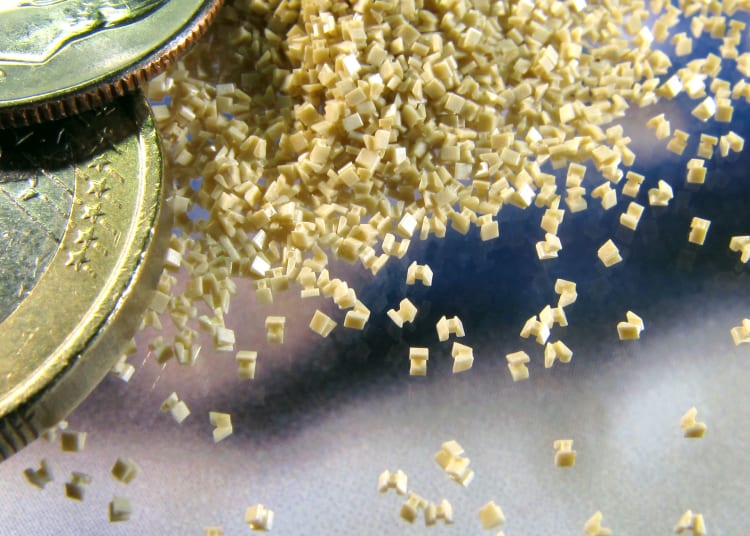
Materials for micro molding
Many relatively standard materials are used in micro molding applications, including but by no means restricted to Polyethylene (PE), Polypropylene (PP), Nylon (Polyamide), Polycarbonate (PC), Delrin (Acetal / Polyoxymethylene / POM), Polysulfone (PSU), and Polybutylene terephthalate (PBT). Micro molding, however, often requires the use of more exotic materials like PEEK, PEI (Ultem®), carbon-filled LCP, or glass-filled nylons which are are commonplace. Soft durometer or elastomeric resins are also prominent. Direct experience with these materials in the context of micro molding is another part of valuable know-how needed to maximize the performance of the resin/part design combination.
Even in macro product design scenarios material selection can be complicated as it is a trade-off between what is best for the functionality of the part or component being designed, and if it is possible to mold it into the shape required. When looking at micro molding applications, however, where limits are often extreme, the issue becomes more complicated.
The typical route to material selection is to match the functional part requirements with material datasheets. However, most datasheets are based on the manufacture of much larger parts, and this will reflect on recommended gate size and flow properties etc…
So some manufacturers looking to micro mold follow datasheets, and then see sub-optimal results when the parts are molded. This can lead to premature design iterations, or in extreme cases the abandonment of projects all together.