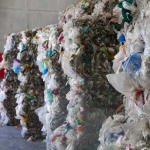
Tomra and a Norwegian waste sorting plant have demonstrated that mixed waste sorting prior to disposal is a superior solution to separate collection. Since it stopped the separate collection for plastics in its region and unleashed the power of mixed waste sorting, the facility increased recovery rates from 28% to 82% and achieved recycling rates of 56,4%, thus meeting the EU’s 2025 recycling targets ahead of time. Today, IVAR ranks first in processing MSW by volume.
Situated in Forus, between the cities of Stavanger and Sandnes in the southwest of Norway, IVAR manages all residues and waste collection from 10 municipalities with an approximate population of 325.000. With its advanced municipal solid waste sorting plant, it recovers high volumes of recyclable materials before incineration, reducing CO2 emissions and the global dependency on virgin material by supplying high-quality recycled content for new products and packaging.
When local and international recycling targets became increasingly stringent, IVAR recognized the need to improve its waste management methods and decided to more closely examine the hidden potential of its region’s household waste. With the goal of finding the most effective and environmentally friendly approach to waste management, the company sought the advice of Tomra. To identify the opportunities in mixed waste sorting and assess its performance potential, the plant sent MSW samples from the region to Tomra’s test facility in Germany. There, these materials underwent extensive tests on the company’s sorting machines. Test analysis showed that, whereas paper recovery from MSW streams performed reasonably well, plastics recovery offered room for improvement. Test analysis unveiled that the household waste contained high amounts of plastic recyclables, even though they were meant to be disposed of separately. The team considered the analysis as a clear call for concrete, future-oriented action.
Embracing new opportunities
Based on the analysis and the still untouched possibilities in MSW sorting, a new business case was developed. The result: the construction of a new fully automated mixed waste sorting plant consisting of new facilities for plastics reprocessing and paper sorting, as well as the elimination of the separate plastics collection in that region. Previously collected separately, plastics are now also disposed of in the grey bin and recovered in the new facility. As a consequence, only the plant’s residues are transported to the waste to energy plant and used for the production of electricity and energy for remote heating systems. In short, the materials discarded by the municipality are turned into value again in the most optimal way.
In late 2014, the plant building project began with Sutco Recycling Technik chosen as a plant supplier for IVAR’s combined residual waste and paper sorting plant. Sutco, in turn, selected Tomra Recycling as project partner for sorting equipment. Since the new facility started operation in January 2019, 22 of Tomra’s state-of-the-art Autosort sorting units efficiently and effectively sort plastics (PET, PS, LDPE, HDPE, PP) and paper (mixed paper, cardboard, beverage cartons) out of the residual waste (grey bins) collected curbside. In addition, metals (aluminum, steel) are recovered from the residual waste.
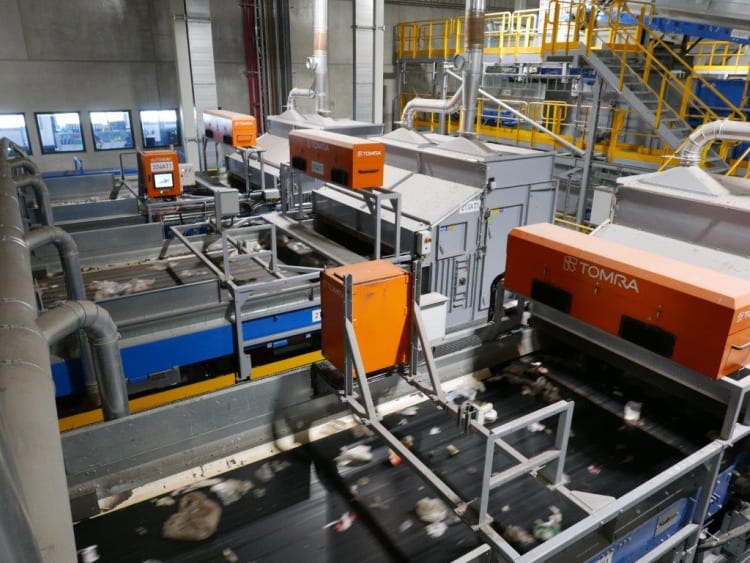
“We have been delighted to be given the opportunity to consult with IVAR in the planning of the new plant, provide our latest sensor-based sorting equipment and accompany such an exciting and game-changing project,”, comments Oliver Lambertz, Tomra Recycling’s Vice President and Head of Business Development. By combining the most advanced processes, plant equipment and sorting technologies, the waste sorting plant has set the following targets: sort nearly all PE, PP, PS or PET plastics suited for (mechanical) recycling; sort 95% of the fractions identified; and realize purity rates of 95-98%.
From mixed waste to recyclable mono fractions
The residual waste generated by the municipalities IVAR serves contains a large amount of valuable and recyclable materials, which in their purest and homogenous form, can be further processed, recycled, and reintroduced into the market as high-quality recyclates. Today, IVAR processes 40 tons of MSW per hour from which paper, plastics, metals, and residues are separated in numerous steps:
Presorting
Once the collected material is fed into the plant, items > 350mm are sorted by a finger screen and shredded into smaller pieces before two drum screens separate the material into three target s: 0-60mm; 60-150mm; and 150-320mm. In a second step, Tomra’s AUTOSORT machines recover 90% of the mid-d (60-150 mm) and the large (150-320 mm) plastic fractions before they extract mixed paper. Finally, magnets and eddy currents remove both the non-ferrous and ferrous metals.
Plastics and paper recovery
After plastics have been presorted, they are further sorted by material type. First, ballistic separators separate plastic film and rigid plastics. Afterwards, 14 Autosort machines undertake the separation of rigid plastics into PP, HDPE, PS, PET and create a clean fraction of LDPE plastic film. To further increase purity levels, these clean material fractions undergo a second sorting step, also carried out by AUTOSORT® machines, to remove the remaining contaminants. The high-quality PS and PET end fractions are then packed into material-type-specific bales and sent to different mechanical recycling plants in Europe. LDPE, HDPE and PP are washed, dried and pelletized in the Forus plant and sold as pellets.
At the same time, the mixed paper fraction, as well as mixed paper and cardboard infeed coming from separate collection, is processed in a separate sorting line. From the 23,250 metric tons of paper sorted per shift, 95,7% of the infeed material is turned into four salable paper products such De-ink, ECC (corrugated cardboard), tetra Pak and carton.