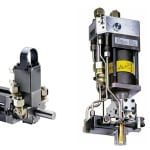
KraussMaffei, world market leader and innovation driver in polyurethane processing machinery, has brought out new, optimized versions of its special mixing heads for the white goods sector. The new versions of the MK 12/18-ULP-2KVVG and MK16/25-ULP-2KVVG transfer mixing heads and the MKE-3B linear mixing head have dramatically improved service lives.
The company embarked on this most intensive redesign project ever for these mixing head models in response to the increasing use of pentane as blowing agent. The very sticky reaction mix produced by pentane systems causes serious wear in processing machinery.
To mitigate the effects of sticky pentane systems, KraussMaffei engineers came up with a new solution for the metal surfaces in contact with the PUR. This is basically a friction-optimized bushing with a specially hardened surface and a patented spiral groove on the cleaning piston. These modifications sharply reduce mixing-head wear, thereby dramatically increasing the number of shots the mixing head is capable of.
When a pentane system is being processed, the foam moulds generally require cleaning with nitrogen. With these transfer mixing heads, the nitrogen can be discharged into the mould via the mixing head discharge tube.
The new version of the MKE-3B mixing head not only boasts a special wear protection, it also operates on the ?T` mixing principle for outstanding mixing performance. One of the PUR components is pumped into the mixing chamber via two nozzles, the other component hits this component stream at right angles. Before pouring into the mould, any turbulence in the well-mixed compound is eliminated as it passes a series of calming pins. This quality engineering makes the MKE-3B the ideal choice for open pouring. Furthermore, it can be relied on to achieve six-figure shot numbers.